煤制甲醇的工艺流程?
今天运困体育就给我们广大朋友来聊聊陕西甲醇厂油雾分离器结构,希望能帮助到您找到想要的答案。
煤制甲醇的工艺流程?
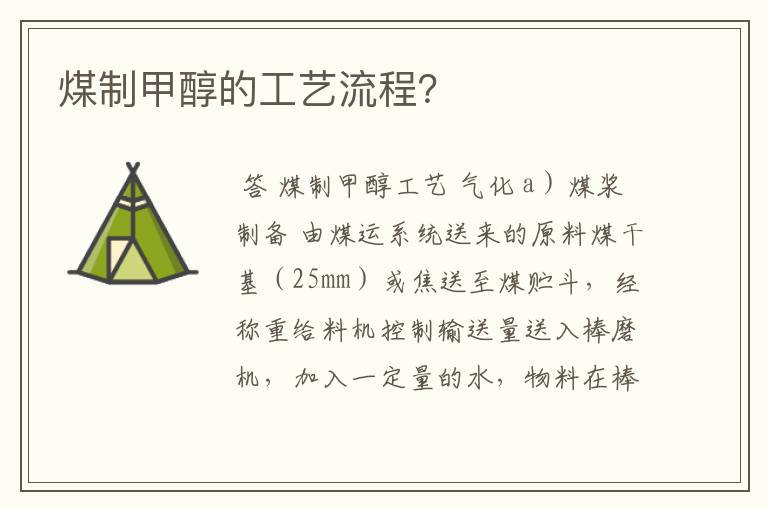
答煤制甲醇工艺
气化
a)煤浆制备
由煤运系统送来的原料煤干基(<25mm)或焦送至煤贮斗,经称重给料机控制输送量送入棒磨机,加入一定量的水,物料在棒磨机中进行湿法磨煤。为了控制煤浆粘度及保持煤浆的稳定性加入添加剂,为了调整煤浆的PH值,加入碱液。出棒磨机的煤浆浓度约65%,排入磨煤机出口槽,经出口槽泵加压后送至气化工段煤浆槽。煤浆制备首先要将煤焦磨细,再制备成约65%的煤浆。磨煤采用湿法,可防止粉尘飞扬,环境好。用于煤浆气化的磨机现在有两种,棒磨机与球磨机;棒磨机与球磨机相比,棒磨机磨出的煤浆粒度均匀,筛下物少。煤浆制备能力需和气化炉相匹配,本项目拟选用三台棒磨机,单台磨机处理干煤量43~53t/h,可满足60万t/a甲醇的需要。
为了降低煤浆粘度,使煤浆具有良好的流动性,需加入添加剂,初步选择木质磺酸类添加剂。
煤浆气化需调整浆的PH值在6~8,可用稀氨水或碱液,稀氨水易挥发出氨,氨气对人体有害,污染空气,故本项目拟采用碱液调整煤浆的PH值,碱液初步采用42%的浓度。
为了节约水源,净化排出的含少量甲醇的废水及甲醇精馏废水均可作为磨浆水。
b)气化
在本工段,煤浆与氧进行部分氧化反应制得粗合成气。
煤浆由煤浆槽经煤浆加压泵加压后连同空分送来的高压氧通过烧咀进入气化炉,在气化炉中煤浆与氧发生如下主要反应:
CmHnSr+m/2O2—→mCO+(n/2-r)H2+rH2S
CO+H2O—→H2+CO2
反应在6.5MPa(G)、1350~1400℃下进行。
气化反应在气化炉反应段瞬间完成,生成CO、H2、CO2、H2O和少量CH4、H2S等气体。
离开气化炉反应段的热气体和熔渣进入激冷室水浴,被水淬冷后温度降低并被水蒸汽饱和后出气化炉;气体经文丘里洗涤器、碳洗塔洗涤除尘冷却后送至变换工段。
气化炉反应中生成的熔渣进入激冷室水浴后被分离出来,排入锁斗,定时排入渣池,由扒渣机捞出后装车外运。
气化炉及碳洗塔等排出的洗涤水(称为黑水)送往灰水处理。
c)灰水处理
本工段将气化来的黑水进行渣水分离,处理后的水循环使用。
从气化炉和碳洗塔排出的高温黑水分别进入各自的高压闪蒸器,经高压闪蒸浓缩后的黑水混合,经低压、两级真空闪蒸被浓缩后进入澄清槽,水中加入絮凝剂使其加速沉淀。澄清槽底部的细渣浆经泵抽出送往过滤机给料槽,经由过滤机给料泵加压后送至真空过滤机脱水,渣饼由汽车拉出厂外。
闪蒸出的高压气体经过灰水加热器回收热量之后,通过气液分离器分离掉冷凝液,然后进入变换工段汽提塔。
闪蒸出的低压气体直接送至洗涤塔给料槽,澄清槽上部清水溢流至灰水槽,由灰水泵分别送至洗涤塔给料槽、气化锁斗、磨煤水槽,少量灰水作为废水排往废水处理。
洗涤塔给料槽的水经给料泵加压后与高压闪蒸器排出的高温气体换热后送碳洗塔循环使用。
2)变换
在本工段将气体中的CO部分变换成H2。
本工段的化学反应为变换反应,以下列方程式表示:
CO+H2O—→H2+CO2
由气化碳洗塔来的粗水煤气经气液分离器分离掉气体夹带的水分后,进入气体过滤器除去杂质,然后分成两股,一部分(约为54%)进入原料气预热器与变换气换热至305℃左右进入变换炉,与自身携带的水蒸汽在耐硫变换催化剂作用下进行变换反应,出变换炉的高温气体经蒸汽过热器与甲醇合成及变换副产的中压蒸汽换热、过热中压蒸汽,自身温度降低后在原料气预热器与进变换的粗水煤气换热,温度约335℃进入中压蒸汽发生器,副产4.0MPa蒸汽,温度降至270℃之后,进入低压蒸汽发生器温度降至180℃,然后进入脱盐水加热器、水冷却器最终冷却到40℃进入低温甲醇洗1#吸收系统。
另一部分未变换的粗水煤气,进入低压蒸汽发生器使温度降至180℃,副产0.7MPa的低压蒸汽,然后进入脱盐水加热器回收热量,最后在水冷却器用水冷却至40℃,送入低温甲醇洗2#吸收系统。
气液分离器分离出来的高温工艺冷凝液送气化工段碳洗塔。
气液分离器分离出来的低温冷凝液经汽提塔用高压闪蒸气和中压蒸汽汽提出溶解在水中的CO2、H2S、NH3后送洗涤塔给料罐回收利用;汽提产生的酸性气体送往火炬。
3)低温甲醇洗
本工段采用低温甲醇洗工艺脱除变换气中CO2、全部硫化物、其它杂质和H2O。
a)吸收系统
本装置拟采用两套吸收系统,分别处理变换气和未变换气,经过甲醇吸收净化后的变换气和未变换气混合,作为甲醇合成的新鲜气。
由变换来的变换气进入原料气一级冷却器、氨冷器、进入分离器,出分离器的变换气与循环高压闪蒸气混合后,喷入少量甲醇,以防止变换气中水蒸气冷却后结冰,然后进入原料气二级冷却器冷却至-20℃,进入变换气甲醇吸收塔,依次脱除H2S+COS、CO2后在-49℃出吸收塔,然后经二级原料气冷却器,一级原料气冷却器复热后去甲醇合成单元。净化气中CO2含量约3.4%,H2S+COS<0.1PPm。
来自甲醇再生塔经冷却的甲醇-49℃从甲醇吸收塔顶进入,吸收塔上段为CO2吸收段,甲醇液自上而下与气体逆流接触,脱除气体中CO2,CO2的指标由甲醇循环量来控制。中间二次引出甲醇液用氨冷器冷却以降低由于溶解热造成的温升。在吸收塔下段,引出的甲醇液大部分进入高压闪蒸器;另一部分溶液经氨冷器冷却后回流进入H2S吸收段以吸收变换气中的H2S和COS,自塔底出来的含硫富液进入H2S浓缩塔。为减少H2和CO损失,从高压闪蒸槽闪蒸出的气体加压后送至变换气二级冷却器前与变换气混合,以回收H2和CO。
未变换气的吸收流程同变换气的吸收流程。
b)溶液再生系统
未变换气和变换气溶液再生系统共用一套装置。
从高压闪蒸器上部和底部分别产生的无硫甲醇富液和含硫甲醇富液进入H2S浓缩塔,进行闪蒸汽提。甲醇富液采用低压氮气汽提。高压闪蒸器上部的无硫甲醇富液不含H2S从塔上部进入,在塔顶部降压膨胀。高压闪蒸器下部的含硫甲醇富液从塔中部进入,塔底加入的氮气将CO2汽提出塔顶,然后经气提氮气冷却器回收冷量后,作为尾气高点放空。
富H2S甲醇液自H2S浓缩塔底出来后进热再生塔给料泵加压,甲醇贫液冷却器换热升温进甲醇再生塔顶部。甲醇中残存的CO2以及溶解的H2S由再沸器提供的热量进行热再生,混和气出塔顶经多级冷却分离,甲醇一级冷凝液回流,二级冷凝液经换热进入H2S浓缩塔底部。分离出的酸性气体去硫回收装置。
从原料气分离器和甲醇再生塔底出来的甲醇水溶液经泵加压后甲醇水分离器,通过蒸馏分离甲醇和水。甲醇水分离器由再沸器提供。塔顶出来的气体送到甲醇再生塔中部。塔底出来的甲醇含量小于100PPm的废水送水煤浆制备工序或去全厂污水处理系统。
c)氨压缩制冷
从净化各制冷点蒸发后的-33℃气氨气体进入氨液分离器,将气体中的液粒分离出来后进入离心式制冷压缩机一段进口压缩至冷凝温度对应的冷凝压力,然后进入氨冷凝器。气氨通过对冷却水放热冷凝成液体后,靠重力排入液氨贮槽。液氨通过分配器送往各制冷设备。
4)甲醇合成及精馏
a)甲醇合成
经甲醇洗脱硫脱碳净化后的产生合成气压力约为5.6MPa,与甲醇合成循环气混合,经甲醇合成循环气压缩机增压至6.5MPa,然后进入冷管式反应器(气冷反应器)冷管预热到235℃,进入管壳式反应器(水冷反应器)进行甲醇合成,CO、CO2和H2在Cu-Zn催化剂作用下,合成粗甲醇,出管壳式反应器的反应气温度约为240℃,然后进入气冷反应器壳侧继续进行甲醇合成反应,同时预热冷管内的工艺气体,气冷反应器壳侧气体出口温度为250℃,再经低压蒸汽发生器,锅炉给水加热器、空气冷却器、水冷器冷却后到40℃,进入甲醇分离器,从分离器上部出来的未反应气体进入循环气压缩机压缩,返回到甲醇合成回路。
一部分循环气作为弛放气排出系统以调节合成循环圈内的惰性气体含量,合成弛放气送至膜回收装置,回收氢气,产生的富氢气经压缩机压缩后作为甲醇合成原料气;膜回收尾气送至甲醇蒸汽加热炉过热甲醇合成反应器副产的中压饱和蒸汽(2.5MPa),将中压蒸汽过热到400℃。
粗甲醇从甲醇分离器底部排出,经甲醇膨胀槽减压释放出溶解气后送往甲醇精馏工段。
系统弛放气及甲醇膨胀槽产生的膨胀气混合送往工厂锅炉燃料系统。
甲醇合成水冷反应器副产中压蒸汽经变换过热后送工厂中压蒸汽管网。
b)甲醇精馏
从甲醇合成膨胀槽来的粗甲醇进入精馏系统。精馏系统由预精馏塔、加压塔、常压塔组成。预精馏塔塔底出来的富甲醇液经加压至0.8MPa、80℃,进入加压塔下部,加压塔塔顶气体经冷凝后,一部分作为回流,一部分作为产品甲醇送入贮存系统。由加压塔底出来的甲醇溶液自流入常压塔下塔进一步蒸馏,常压塔顶出来的回流液一部分回流,一部分作为精甲醇经泵送入贮存系统。常压塔底的含甲醇的废水送入磨煤工段作为磨煤用水。在常压塔下部设有侧线采出,采出甲醇、乙醇和水的混合物,由汽提塔进料泵送入汽提塔,汽提塔塔顶液体产品部分回流,其余部分作为产品送至精甲醇中间槽或送至粗甲醇贮槽。汽提塔下部设有侧线采出,采出部分异丁基油和少量乙醇,混合进入异丁基油贮槽。汽提塔塔底排出的废水,含少量甲醇,进入沉淀池,分离出杂醇和水,废水由废水泵送至废水处理装置。
c)中间罐区
甲醇精馏工序临时停车时,甲醇合成工序生产的粗甲醇,进入粗甲醇贮罐中贮存。甲醇精馏工序恢复生产时,粗甲醇经粗甲醇泵升压后送往甲醇精馏工序。
甲醇精馏工序生产的精甲醇,进入甲醇计量罐中。经检验合格的精甲醇用精甲醇泵升压送往成品罐区甲醇贮罐中贮存待售。
5)空分装置
本装置工艺为分子筛净化空气、空气增压、氧气和氮气内压缩流程,带中压空气增压透平膨胀机,采用规整填料分馏塔,全精馏制氩工艺。
原料空气自吸入口吸入,经自洁式空气过滤器除去灰尘及其它机械杂质。过滤后的空气进入离心式空压机经压缩机压缩到约0.57MPa(A),然后进入空气冷却塔冷却。冷却水为经水冷塔冷却后的水。空气自下而上穿过空气冷却塔,在冷却的同时,又得到清洗。
经空冷塔冷却后的空气进入切换使用的分子筛纯化器空气中的二氧化碳、碳氢化合物和水分被吸附。分子筛纯化器为两只切换使用,其中一只工作时,另一只再生。纯化器的切换周期约为4小时,定时自动切换。
净化后的空气抽出一小部分,作为仪表空气和工厂空气。
其余空气分成两股,一股直接进入低压板式换热器,从换热器底部抽出后进入下塔。另外一股进入空气增压机。
经过空气增压机的中压空气分成两部分,一部分进入高压板式换热器,冷却后进入低温膨胀机,膨胀后空气进入下塔精馏。另一部分中压空气经过空气增压机二段压缩为高压空气,进入高压板式换热器,冷却后经节流阀节流后进入下塔。
空气经下塔初步精馏后,获得富氧液空、低纯液氮、低压氮气,其中富氧液空和低纯液氮经过冷器过冷后节流进入上塔。经上塔进一步精馏后,在上塔底部获得液氧,并经液氧泵压缩后进入高压板式换热器,复热后出冷箱,进入氧气管网。
在下塔顶部抽取的低压氮气,进入高压板式换热器,复热后送至全厂低压氮气管网。
从上塔上部引出污氮气经过冷器、低压板式换热器和高压板式换热器复热出冷箱后分成两部分:一部分进入分子筛系统的蒸汽加热器,作为分子筛再生气体,其余污氮气去水冷塔。
从上塔中部抽取一定量的氩馏份送入粗氩塔,粗氩塔在结构上分为两段,第二段氩塔底部的回流液经液体泵送入第一段顶部作为回流液,经粗氩塔精馏得到99.6Ar,2ppmO2的粗氩,送入精氩塔中部,经精氩塔精馏在精氩塔底部得到纯度为99.999%Ar的**氩作为产品抽出送入进贮槽。
甲醇是怎样练成
答生产甲醇的方法有多种,早期用木材或木质素干馏法制甲醇的方法,今天在工业上已经被淘汰了.氯甲烷水解法也可以生产甲醇,但因水解法价格昂贵,没有得到工业上的应用.甲烷部分氧化法可以生产甲醇,这种制甲醇的方法工艺流程简单,建设投资节省,但是,这种氧化过程不易控制,常因深度氧化生成碳的氧化物和水.而使原料和产品受到很大损失.因此甲烷部分氧化法制甲醇的方法仍未实现工业化.但它具有上述优点,国外在这方面的研究—直没有中断.应该是一个很有工业前途的制取甲醇的方法.
目前工业上几乎都是采用一氧化碳、二氧化碳加压催化氢化法合成甲醇.典型的流程包括原料气制造、原料气净化、甲醇合成、粗甲醇精馏等工序.
天然气、石脑油、重油、煤及其加工产品(焦炭、焦炉煤气)、乙炔尾气等均可作为生产甲醇合成气的原料.天然气与石脑油的蒸气转化需在结构复杂造价很高的转化炉中进行.转化炉设置有辐射室与对流室,在高温,催化剂存在下进行烃类蒸气转化反应.重油部分氧化需在高温气化炉中进行.以固体燃料为原料时,可用间歇气化或连续气化制水煤气.间歇气化法以空气、蒸汽为气化剂,将吹风、制气阶段分开进行,连续气化以氧气、蒸汽为气化剂,过程连续进行.
甲醇生产中所使用的多种催化剂,如天然气与石脑油蒸气转化催化剂、甲醇合成催化剂都易受硫化物毒害而失去活性,必须将硫化物除净.气体脱硫方法可分为两类,一类是干法脱硫,一类是湿法脱硫.干法脱硫设备简单,但由于反应速率较慢,设备比较庞大.湿法脱硫可分为物理吸收法、化学吸收法与直接氧化法三类.
甲醇的合成是在高温、高压、催化剂存在下进行的,是典型的复合气-固相催化反应过程.随着甲醇合成催化剂技术的不断发展,目前总的趋势是由高压向低、中压发展.
粗甲醇中存在水分、高级醇、醚、酮等杂质,需要精制.精制过程包括精馏与化学处理.化学处理主要用碱破坏在精馏过程中难以分离的杂质,并调节PH.精馏主要是除去易挥发组分,如二甲醚、以及难以挥发的组分,如乙醇高级醇、水等.
甲醇生产的总流程长,工艺复杂,根据不同原料与不同的净化方法可以演变为多种生产流程.
2.简述高压法、中压法、低压法三种方法及区别
高压工艺流程一般指的是使用锌铬催化剂,在300—400℃,30MPa高温高压下合成甲醇的过程.自从1923年第一次用这种方法合成甲醇成功后,有50年的时间,世界上合成甲醇生产都沿用这种方法,仅在设计上有某些细节不同,例如甲醇合成塔内移热的方法有冷管型连续换热式和冷激型多段换热式两大类,反应气体流动的方式有轴向和径向或者二者兼有的混合型式,有副产蒸汽和不副产蒸汽的流程等.近几年来,我国开发了25-27MPa压力下在铜基催化剂上合成甲醇的技术,出口气体中甲醇含量4%左右,反应温度230-290℃.
ICl低压甲醇法为英国ICl公司在1966年研究成功的甲醇生产方法.从而打破了甲醇合成的高压法的垄断,这是甲醇生产工艺上的一次重大变革,它采用51-1型铜基催化剂,合成压力5MPa.ICl法所用的合成塔为热壁多段冷激式,结构简单,每段催化剂层上部装有菱形冷激气分配器,使冷激气均匀地进入催化剂层,用以调节塔内温度.低压法合成塔的型式还有联邦德国Lurgi公司的管束型副产蒸汽合成塔及美国电动研究所的三相甲醇合成系统.70年代,我国轻工部四川维尼纶厂从法国Speichim公司引进了一套以乙炔尾气为原料日产300吨低压甲醇装置(英国ICI专利技术).80年代,齐鲁石化公司第二化肥厂引进了联邦德国Lurge公司的低压甲醇合成装置.
中压法是在低压法研究基础上进一步发展起来的,由于低压法操作压力低,导致设备体积相当庞大,不利于甲醇生产的大型化.因此发展了压力为10MPa左右的甲醇合成中压法.它能更有效地降低建厂费用和甲醇生产成本.例如ICI公司研究成功了51-2型铜基催化剂,其化学组成和活性与低压合成催化剂51-1型,只是催化剂的晶体结构不相同,制造成本比51-1型高贵.由于这种催化剂在较高压力下也能维持较长的寿命,从而使ICI公司有可能将原有的5MPa的合成压力提高到l0MPa,所用合成塔与低压法相同也是四段冷激式,其流程和设备与低压法类似.
3.简述天然气制甲醇的生产方法:
天然气是制造甲醇的主要原料.天然气的主要组分是甲烷,还含有少量的其他烷烃、烯烃与氮气.以天然气生产甲醇原料气有蒸汽转化、催化部分氧化、非催化部分氧化等方法,其中蒸汽转化法应用得最广泛,它是在管式炉中常压或加压下进行的.由于反应吸热必须从外部供热以保持所要求的转化温度,一般是在管间燃烧某种燃料气来实现,转化用的蒸汽直接在装置上靠烟道气和转化气的热量制取.
由于天然气蒸汽转化法制的合成气中,氢过量而一氧化碳与二氧化碳量不足,工业上解决这个问题的方法一是采用添加二氧化碳的蒸汽转化法,以达到合适的配比,二氧化碳可以外部供应,也可以由转化炉烟道气中回收.另一种方法是以天然气为原料的二段转化法,即在第一段转化中进行天然气的蒸汽转化,只有约1/4的甲烷进行反应,第二段进行天然气的部分氧化,不仅所得合成气配比合适而且由于第二段反应温度提高到800℃,残留的甲烷量可以减少,增加了合成甲醇的有效气体组分.
天然气进入蒸汽转化炉前需进行净化处理清除有害杂质,要求净化后气体含硫量小于0.1mL/m3.转化后的气体经压缩去合成工段合成甲醇.
4.简述煤、焦炭制甲醇的生产方法.
煤与焦炭是制造甲醇粗原料气的主要固体燃料.用煤和焦炭制甲醇的工艺路线包括燃料的气化、气体的脱硫、变换、脱碳及甲醇合成与精制.
用蒸汽与氧气(或空气、富氧空气)对煤、焦炭进行热加工称为固体燃料气化,气化所得可燃性气体通称煤气是制造甲醇的初始原料气,气化的主要设备是煤气发生炉,按煤在炉中的运动方式,气化方法可分为固定床(移动床)气化法、流化床气化法和气流床气化法.国内用煤与焦炭制甲醇的煤气化——般都沿用固定床间歇气化法,煤气炉沿用
UCJ炉.在国外对于煤的气化,目前已工业化的煤气化炉有柯柏斯-托切克(Koppers-Totzek)、鲁奇(Lurge)及温克勒(Winkler)三种.还有第二、第三代煤气化炉的炉型主要有德士古(Texaco)及谢尔-柯柏斯(Shell--Koppers)等.
用煤和焦炭制得的粗原料气组分中氢碳比太低,故在气体脱硫后要经过变换工序.使过量的一氧化碳变换为氢气和二氧化碳,再经脱碳工序将过量的二氧化碳除去.
原料气经过压缩、甲醇合成与精馏精制后制得甲醇.
5.简述油制甲醇的生产方法.
工业上用油来制取甲醇的油品主要有二类:一类是石脑油,另一类是重油.
原油精馏所得的220℃以下的馏分称为轻油,又称石脑油.以石脑油为原料生产合成气的方法有加压蒸汽转化法,催化部分氧化法、加压非催化部分氧化法、间歇催化转化法等.目前用石脑油生产甲醇原料气的主要方法是加压蒸汽转化法.石脑油的加压蒸汽转化需在结构复杂的转化炉中进行.转化炉设置有辐射室与对流室,在高温、催化剂存在下进行烃类蒸汽转化反应.石脑油经蒸汽转化后,其组成恰可满足合成甲醇之需要.既无需在转化前后补加二氧化碳或设二段转化,也无需经变换、脱碳调整其组成.
重油是石油炼制过程中的一种产品,根据炼制方法不同,可分为常压重油、减压重油、裂化重油及它们的混合物.以重油为原料制取甲醇原料气有部分氧化法与高温裂解法两种途径.裂解法需在1400℃的高温下,在蓄热炉中将重油裂解,虽然可以不用氧气,但设备复杂,操作麻烦,生成炭黑量多.
重油部分氧化是指重质烃类和氧气进行燃烧反应,反应放热,使部分碳氢化合物发生热裂解,裂解产物进一步发生氧化、重整反应,最终得到以H2、CO为主,及少量CO2、CH4的合成气供甲醇合成使用.重油部分氧化法所生成的合成气,由于原料重油中碳氢比高,合成气中一氧化碳与二氧化碳含量过量,需将部分合成气经过变换,使一氧化碳与水蒸气作用生成氢气与二氧化碳,然后脱除二氧化碳,以达到合成甲醇所需之组成.
合成后的粗甲醇需经过精制,除去杂质与水,得到精甲醇.
6.简述联醇生产方法.
与合成氨联合生产甲醇简称联醇,这是一种合成气的净化工艺,以替代我国不少合成氨生产用铜氨液脱除微量碳氧化物而开发的一种新工艺.
联醇生产的工艺条件是在压缩机五段出口与铜洗工序进口之间增加一套甲醇合成的装置,包括甲醇合成塔、循环机、水冷器、分离器和粗甲醇贮槽等有关设备,工艺流程是压缩机五段出口气体先进人甲醇合成塔,大部分原先要在铜洗工序除去的一氧化碳和二氧化碳在甲醇合成塔内与氢气反应生成甲醇,联产甲醇后进入铜洗工序的气体一氧化碳含量明显降低,减轻了铜洗负荷,同时变换工序的一氧化碳指标可适量放宽,降低了变换的蒸汽消耗,而且压缩机前几段气缸输送的一氧化碳成为有效气体,压缩机电耗降低.
联产甲醇后能耗降低较明显,可使每吨氨节电50kw.h,节省蒸汽0.4t,折合能耗为200万kJ.联醇工艺流程必须重视原料气的精脱硫和精馏等工序,以保证甲醇催化剂使用寿命和甲醇产品质量.
甲醇生产工艺的生产方法
答天然气制甲醇
天然气是制造甲醇的主要原料.天然气的主要组分是甲烷,还含有少量的其他烷烃、烯烃与氮气.以天然气生产甲醇原料气有蒸汽转化、催化部分氧化、非催化部分氧化等方法,其中蒸汽转化法应用得最广泛,它是在管式炉中常压或加压下进行的.由于反应吸热必须从外部供热以保持所要求的转化温度,一般是在管间燃烧某种燃料气来实现,转化用的蒸汽直接在装置上靠烟道气和转化气的热量制取.
由于天然气蒸汽转化法制的合成气中,氢过量而一氧化碳与二氧化碳量不足,工业上解决这个问题的方法一是采用添加二氧化碳的蒸汽转化法,以达到合适的配比,二氧化碳可以外部供应,也可以由转化炉烟道气中回收.另一种方法是以天然气为原料的二段转化法,即在第一段转化中进行天然气的蒸汽转化,只有约1/4的甲烷进行反应,第二段进行天然气的部分氧化,不仅所得合成气配比合适而且由于第二段反应温度提高到800℃,残留的甲烷量可以减少,增加了合成甲醇的有效气体组分.
天然气进入蒸汽转化炉前需进行净化处理清除有害杂质,要求净化后气体含硫量小于0.1mL/m3.转化后的气体经压缩去合成工段合成甲醇.
煤、焦炭制甲醇
煤与焦炭是制造甲醇粗原料气的主要固体燃料.用煤和焦炭制甲醇的工艺路线包括燃料的气化、气体的脱硫、变换、脱碳及甲醇合成与精制.
用蒸汽与氧气(或空气、富氧空气)对煤、焦炭进行热加工称为固体燃料气化,气化所得可燃性气体通称煤气是制造甲醇的初始原料气,气化的主要设备是煤气发生炉,按煤在炉中的运动方式,气化方法可分为固定床(移动床)气化法、流化床气化法和气流床气化法.国内用煤与焦炭制甲醇的煤气化——般都沿用固定床间歇气化法,煤气炉沿用 UCJ炉.在国外对于煤的气化,已工业化的煤气化炉有柯柏斯-托切克(Koppers-Totzek)、鲁奇(Lurge)及温克勒(Winkler)三种.还有第二、第三代煤气化炉的炉型主要有德士古(Texaco)及谢尔-柯柏斯(Shell--Koppers)等.
用煤和焦炭制得的粗原料气组分中氢碳比太低,故在气体脱硫后要经过变换工序.使过量的一氧化碳变换为氢气和二氧化碳,再经脱碳工序将过量的二氧化碳除去.
原料气经过压缩、甲醇合成与精馏精制后制得甲醇.
油制甲醇
工业上用油来制取甲醇的油品主要有二类:一类是石脑油,另一类是重油.
原油精馏所得的220℃以下的馏分称为轻油,又称石脑油.以石脑油为原料生产合成气的方法有加压蒸汽转化法,催化部分氧化法、加压非催化部分氧化法、间歇催化转化法等.用石脑油生产甲醇原料气的主要方法是加压蒸汽转化法.石脑油的加压蒸汽转化需在结构复杂的转化炉中进行.转化炉设置有辐射室与对流室,在高温、催化剂存在下进行烃类蒸汽转化反应.石脑油经蒸汽转化后,其组成恰可满足合成甲醇之需要.既无需在转化前后补加二氧化碳或设二段转化,也无需经变换、脱碳调整其组成.
重油是石油炼制过程中的一种产品,根据炼制方法不同,可分为常压重油、减压重油、裂化重油及它们的混合物.以重油为原料制取甲醇原料气有部分氧化法与高温裂解法两种途径.裂解法需在1400℃的高温下,在蓄热炉中将重油裂解,虽然可以不用氧气,但设备复杂,操作麻烦,生成炭黑量多.
重油部分氧化是指重质烃类和氧气进行燃烧反应,反应放热,使部分碳氢化合物发生热裂解,裂解产物进一步发生氧化、重整反应,最终得到以H2、CO为主,及少量CO2、CH4的合成气供甲醇合成使用.重油部分氧化法所生成的合成气,由于原料重油中碳氢比高,合成气中一氧化碳与二氧化碳含量过量,需将部分合成气经过变换,使一氧化碳与水蒸气作用生成氢气与二氧化碳,然后脱除二氧化碳,以达到合成甲醇所需之组成.
合成后的粗甲醇需经过精制,除去杂质与水,得到精甲醇.
联醇生产
与合成氨联合生产甲醇简称联醇,这是一种合成气的净化工艺,以替代我国不少合成氨生产用铜氨液脱除微量碳氧化物而开发的一种新工艺.
联醇生产的工艺条件是在压缩机五段出口与铜洗工序进口之间增加一套甲醇合成的装置,包括甲醇合成塔、循环机、水冷器、分离器和粗甲醇贮槽等有关设备,工艺流程是压缩机五段出口气体先进人甲醇合成塔,大部分原先要在铜洗工序除去的一氧化碳和二氧化碳在甲醇合成塔内与氢气反应生成甲醇,联产甲醇后进入铜洗工序的气体一氧化碳含量明显降低,减轻了铜洗负荷,同时变换工序的一氧化碳指标可适量放宽,降低了变换的蒸汽消耗,而且压缩机前几段气缸输送的一氧化碳成为有效气体,压缩机电耗降低.
联产甲醇后能耗降低较明显,可使每吨氨节电50kw.h,节省蒸汽0.4t,折合能耗为200万kJ.联醇工艺流程必须重视原料气的精脱硫和精馏等工序,以保证甲醇催化剂使用寿命和甲醇产品质量。
国内甲醇价格
据2012年11月23日中国化工产品网消息,国内甲醇价格基本平稳,几大主要产地出厂价格和贸易商出货价格波动不大,行情稳定。甲醇生产主要厂家出厂价平稳:东北黑龙江煤制及焦炉气制甲醇企业出厂价格在2650-2750元/吨;内蒙主要企业甲醇出厂价格基本稳定在2120-2150元/吨;陕北主要甲醇企业出厂价格2130-2160元/吨;陕西关中甲醇企业省外出厂主流2400-2450元/吨。甲醇主要市场交易价格也行情稳定:华南港口甲醇出罐报价在2840-2850元/吨,市场整体成交情况平淡;河南甲醇市场局部下滑,豫北主流成交2600元/吨,豫西地区2600元/吨,洛阳贸易商主流出罐在2590元/吨左右;西南甲醇市场稳定,其中主流出厂价格2400-2700元/吨,贸易商出货价格2750元/吨。
焦化厂和洗煤厂的设备与工艺流程,
答焦化厂工艺流程
焦化厂的生产工艺
焦化厂有9个生产车间,分别为备煤车间、一号炼焦车间、二号炼焦车间、运焦车间、一回收车间、二回收车间、热力车间、维修车间和精制车间。焦化厂主要生产车间:备煤车间、炼焦车间、煤气净化车间及其公辅设施等,各车间主要生产设施如下表所示:
序号
系统名称
主要生产设施
1
备煤车间
煤仓、配煤室、粉碎机室、皮带机运输系统、煤制样室
2
炼焦车间
煤塔、焦炉、装煤设施、推焦设施、拦焦设施、熄焦塔、筛运焦工段(包括焦台、筛焦楼)
3
煤气净化车间
冷鼓工段(包括风机房、初冷器、电捕焦油器等设施);脱氨工段(包括洗氨塔、蒸氨塔、氨分解炉等设施);粗苯工段(包括终冷器、洗苯塔、脱苯塔等设施)
4
公辅设施
废水处理站、供配电系统、给排水系统、综合水泵房、备煤除尘系统、筛运焦除尘系统、化验室等设施、制冷站等
3、炼焦的重要意义
由高温炼焦得到的焦炭可供高炉冶炼、铸造、气化和化工等工业部门作为燃料和原料;炼焦过程中得到的干馏煤气经回收、精制可得到各种芳香烃和杂环混合物,供合成纤维、医药、染料、涂料和国防等工业做原料;经净化后的焦炉煤气既是高热值燃料,也是合成氨、合成燃料和一系列有机合成工业的原料。因此,高温炼焦不仅是煤综合利用的重要途径,也是冶金工业的重要组成成分。
政策性风险煤炭是我国最重要的能源之一在国民经济运行中处于举足轻重的地位焦化行业属于国家重点扶持的行业。为建立大型钢铁循环结构,在钢铁的重要生产基地和炼焦煤生产基地建设并经营现代化大型焦化厂符合我国产业政策和经济结构调整方向也是焦化工业发展的一个前景。
五、原料煤的准备
备煤车间的生产任务是给炼焦车间提供数量充足、质量合乎要求的配合煤。其工艺流程为:原料煤→受煤坑→煤场→斗槽→配煤盘→粉碎机→煤塔。
1、煤的接收与储存
原料煤一般以汽车火车的方式从各地运输过来,邯钢焦化厂的原料煤主要来自邢台的康庄、官庄,峰峰和山西等地。当汽车、火车到达后,与受煤坑定位后,用螺旋卸煤机把煤卸到料仓里,当送料小车开启料仓开口后,用皮带把煤料运到规定位置。注意:每个料仓一次只能盛放同一种类别的煤。
为了保证焦炉的连续生产和稳定焦炉煤的质量,应根据煤质的类别用堆取料机把运来的煤卸放在煤场的各规定位置。邯钢焦化厂的备煤车间用的气煤、肥煤、焦煤和瘦煤四种,按规定分别堆放在煤场的五个区。
2、煤原料的特性及配煤原则
①气煤 气煤的煤化程度比长焰煤高,煤的分子结构中侧链多且长,含氧量高。在热解过程中,不仅侧链从缩合芳环上断裂,而且侧链本身又在氧键处断裂,所以生成了较多的胶质体,但黏度小,流动性大,其热稳定性差,容易分解。在生成半焦时,分解出大量的挥发性气体,能够固化的部分较少。当半焦转化成焦炭时,收缩性大,产生了很多裂纹,大部分为纵裂纹,所以焦炭细长易碎。
在配煤中,气煤含量多,将使焦炭块度降低,强度低。但配以适当的气煤,可以增加焦炭的收缩性,便于推焦,又保护了炉体,同时可以得到较多的化学产品。由于中国气煤储存量大,为了合理的利用炼焦煤的资源,在炼焦时应尽量多配气煤。
②肥煤 肥煤的煤化程度比气煤高,属于中等变质程度的煤。从分子结构看,肥煤所含的侧链较多,但含氧量少,隔绝空气加热时能产生大量的相对分子质量较大的液态产物,因此,肥煤产生的胶质体数量最多,其最大胶质体厚度可达25mm,并具有良好的流动性,且热稳定性也好。肥煤胶质体生成温度为320℃,固化温度为460℃,处于胶质体状态的温度间隔为140℃。如果升温为3℃/min,胶质体的存在时间可达50min,因此决定了肥煤黏结性最强,是中国炼焦煤的基础煤种之一。由于挥发性高,半焦的热分解和热缩聚都比较剧烈,最终收缩量很大,所以生成焦炭的类问较多,又深又宽,且多以横裂纹出现,故易碎成小块,耐磨性差,高挥发性的肥煤炼出的焦炭的耐磨强度更差一些。肥煤单独炼焦时,由于胶质体数量多,又有一定的黏结性,膨胀性较大,导致推焦困难。
在配煤中,加入肥煤后,可起到提高黏结性的作用,所以肥煤是炼焦配煤中的重要组分,并为多配入黏结性较差的煤提供了条件。
③焦煤 焦煤的变质程度比肥煤稍高,挥发性比肥煤低,分子结构中大分子侧链比肥煤少,含氧量较低。热分解时产生的液态产物比肥煤少,但热稳定性更高,胶质体数量多,黏性大,固化温度较高,半焦收缩量和收缩均较小,所以炼焦出的焦炭不仅耐磨强度高、焦块大、裂纹少,而且抗碎强度也好。就结焦性而言,焦煤是最好的能炼制出高质量焦炭的煤。
配煤时,焦煤的配入量可在较宽的范围内波动,且能获得强度较高的焦炭。所以配入焦煤的目的是增加焦炭的强度。
④瘦煤 瘦煤的煤化程度较高,是低挥发性的中等变质程度的黏结性煤,加热时生成的胶质体少,黏度大。单独炼焦时,能得到块度大、裂纹少、抗碎强度高的焦炭,但焦炭的熔融性很差,焦炭的耐磨性也差。在配煤时配入瘦煤可以提高焦炭的块度,作为炼焦配煤效果较好。
为了保证焦炭的质量,利于生产操作,配煤应遵循以下原则:
①配合煤的性质与本厂的煤料预处理工艺以及炼焦条件相适应,保证炼出的焦炭质量符合规定的技术质量指标,满足用户的需求。
②焦炉生产中,注意不要产生过大的膨胀压力,在结焦末期要有足够的收缩度,避免推焦困难和损坏炉体。
③充分利用本地区的资源,做到运输合理,尽量缩短煤源的平均距离,便于车辆的调配,降低生产成本。
④在尽可能的情况下,适当多配一些高挥发性的煤,以增加化学产品的产率。
⑤在保证煤炭质量的前提下,应多配气煤等弱黏结性煤,尽量少用优质焦煤,努力做到合理利用中国的煤炭资源。
3、配煤过程
当需要哪种煤时,用堆取料机通过皮带把煤输送到斗槽里,斗槽里的煤再次通过皮带送向配煤盘按要求进行配煤。邯钢焦化厂配煤比一般为:气煤28%,焦煤45%,肥煤18%,瘦煤9%。在进行配煤时,邯钢焦化厂采用的是利用核子秤进行衰减,通过信号的转换传到电脑上进行控制的。信号控制流程为:Cs-137→煤料→(衰减)电离室→(惰性气体)电流→放大器、变送单元→称重频率信号、变速信号→电脑系统。
4、煤的粉碎
邯钢焦化厂备煤车间的原料煤的精细度为70%~80%,含义为<3mm的煤料占总重量的百分数。在进入粉碎机之前,一部分达到原料煤细度的煤直接由皮带运往煤塔,另一部分未达标的由配煤工段运来的配合煤则先经除铁装置将煤料中的铁件吸净后进入粉碎机,再由皮带运往煤塔。在邯钢焦化厂的配煤车间用的是可逆锤式粉碎机,在粉碎机旁还设有除尘装置。
5、备煤车间设备简介
螺旋卸煤机:旋转机构、提升机构、走行机构、机架。
堆取料机:取料机构、回转机构、变幅机构、悬臂皮带机、尾车、走行机构。
斗槽;南斗槽供1#-4#焦炉 有8个仓库 每个仓库500吨;北斗槽供5#-6#焦炉,有8个仓库 每个仓库500吨。
配煤盘:圆盘、刮料机、加减套筒、减速机、电机。
粉碎机:转子、锤头。
六、炼焦
所谓高温炼焦,就是煤在隔绝空气加热到950-1050℃,经过干燥、热解、熔融、黏结、固化、收缩等过程最终得到焦炭。
1、炼焦生产工艺流程
由备煤车间送来的配合煤装入煤塔,装煤车按作业计划从煤塔取煤,经计量后装入炭化室内。煤料在炭化室内经过一个结焦周期的高温干馏制成焦炭并产生荒煤气。
炭化室内的焦炭成熟后,用推焦车推出,经拦焦车导入熄焦车内,并由电机车牵引熄焦车到熄焦塔内进行喷水熄焦。熄焦后的焦炭卸至凉焦台上,冷却一定时间后送往筛焦工段,经筛分按级别贮存待运。
煤在炭化室干馏过程中产生的荒煤气汇集到炭化室顶部空间,经过上升管、桥管进入集气管。约700℃左右的荒煤气在桥管内被氨水喷洒冷却至90℃左右。荒煤气中的焦油等同时被冷凝下来。煤气和冷凝下来的焦油等同氨水一起经过吸煤气管送入煤气净化车间。
焦炉加热用的焦炉煤气,由外部管道架空引入。焦炉煤气经预热后送到焦炉地下室,通过下喷管把煤气送入燃烧室立火道底部与由废气交换开闭器进入的空气汇合燃烧。燃烧后的废气经过立火道顶部跨越孔进入下降气流的立火道,再经蓄热室,又格子赚把废气的部分显热回收后,经过小烟道、废气交换开闭器、分烟道、总烟道、烟囱排入大气。
2、焦炉结构分析
焦炉结构的变化与发展主要是为了更好的解决焦饼高向与长向的加热均匀性,节能降耗、降低投资成本,提高经济效益。为了保证焦炭、煤气的质量和产量,不仅需要有合适的配煤比,而且要有良好的外部条件,而合理的焦炉结构就是用来保证外部条件的手段。为此,需从焦炉结构的各个部位加以分析。邯钢焦化厂采用的是JN43-58-Ⅱ型焦炉和JN43-80型焦炉。
现代焦炉炉体最上部是炉顶,炉顶之下为相间配置的燃烧室和炭化室,炉体下部有蓄热室和连接蓄热室和燃烧室的斜道区,每个蓄热室下部的小烟道通过交换开闭器与烟道连接。烟道设在焦炉基础内或基础两侧,烟道末端通向烟囱。因此焦炉由三室两区组成,即炭化室、燃烧室、蓄热室、斜道区、炉顶区和基础部分。因为JN43-80型焦炉是在JN43-58-Ⅱ型焦炉的基础上,通过多年的生产实践,进一步完善改进而来的,所以下面以JN43-58-Ⅱ型焦炉为例将焦炉的部分做下分析。
1)炭化室
炭化室是接受煤料并对装炉煤料隔绝空气进行干馏焦碳的炉室,一般由硅质耐火材料砌筑而成。炭化室位于两侧燃烧室之间,顶部由3-4个加煤孔,并有1-2个导出干馏煤气的上升管,它的两端为内衬耐火材料的铸铁炉门。JN43-58-Ⅱ型焦炉的炭化室尺寸分为两种宽度,即平均宽为407mm和450mm两种形式,炭化室全高为4300mm,全长为14080mm,有效长为13350mm,炭化室的有效面积为21.7m3加热水平高度为800mm。
2)燃烧室
燃烧室位于炭化室两侧,是煤气燃烧的地方,煤气与空气在其中混合燃烧,产生的热量传给炉墙,间接加热炭化室中煤料,对其进行高温干馏。燃烧室一般用硅砖砌筑。JN43-58-Ⅱ型焦炉燃烧室宽度为736mm和693mm(包括炉墙),炉墙为厚度为100mm的带舌槽的硅砖砌筑。燃烧室属于双联火道带废气循环式结构,它有28个立火道组成,相邻火道的中心距为480mm,立火道隔墙厚度为130 mm。其中成对的隔墙上部有跨越孔,下部取消了边火道的循环孔,防止了短路。立火道底部的两个斜道区出口设置在燃烧室中心线的两侧,在JN43-58-Ⅱ型焦炉基础上加大边斜道口的断面积,保证了两端炉头的供气量。
3)蓄热室
蓄热室作用就是利用蓄积废气的热量来预热燃烧所需的空气和贫煤气。JN43-58-Ⅱ型焦炉每个炭化室底部有两个蓄热室,一个为煤气蓄热室,另一个为空气蓄热室。它们同时和其侧上放的两个燃烧室相连。燃烧室正下方为主墙,主墙内有垂直砖煤气道,焦炉煤气由地下室煤气与主管经此道送入立火道底部与空气混合燃烧。由于主墙两侧气流导向,中间又有砖煤气道,压差大容易串漏。故砖煤气道系用内径为50mm的管砖,管砖外用带舌槽的异型砖交错砌成厚为270mm的主墙。蓄热室洞宽为321.5mm,内放17层九孔薄壁式格子砖。为使蓄热室长向气流均匀分布,采用扩散式箅子砖,配置不同孔径的扩散或收缩孔型,蓄热室隔墙均用硅砖砌筑,且其内表面衬有黏土砖。
4)斜道区
连接蓄热室和燃烧室的通道为斜道区,它位于蓄热室顶部和燃烧室底部之间,用于导入空气和煤气,并将其分配到每个立火道中,同时排除废气。燃烧室的每个立火道与其相应的斜道相连,当用焦炉煤气加热时,由两个斜道送入空气和导出废气,而焦炉煤气由垂直砖煤气道进入。当用贫煤气加热时,一个斜道送入煤气,另一个斜道送入空气,换向后两个斜道均导出废气。斜道口布置调节砖,在确定斜道断面尺寸时,一般应使斜道口阻力占上升气流斜道总阻力的2/3-3/4;为了保持炉头温度,应使炉头斜道出口断面比中部大50%-60%;斜道口的倾斜角一般不应低于30 ,斜道断面逐渐缩小的夹角一般小于7 等等。
5)基础平台
基础平台位于炉体底部,它支撑整个炉体,炉体设施和机械的质量,并把它传到地基上。JN43-58-Ⅱ型焦炉基础为下喷式,又底板、顶板和支柱组成,用钢筋混凝土浇铸而成。为了减轻温度对基础的影响,焦炉砌体的下部与基础平台之间有4-6层红砖。
6)炉顶区
JN43-58-Ⅱ型焦炉炉顶区砌有装煤孔、上升管孔、看火孔、洪炉孔和拉条钩等。炉顶的实心部分由砌炉过程中的废耐火砖砌筑,炉顶表面用耐磨性好、能抵抗雨水侵蚀的缸砖砌筑。
总之,JN43-58-Ⅱ型焦炉的结构特点是:双联火道带废气循环,焦炉煤气下喷,两格蓄热室的复热式焦炉,具有结构严密、炉头不易开裂、高向加热均匀、热工效率高、砖型少、挥发性低等优点。
3、护炉机械设备
焦炉四大车有:装煤车、推焦车、拦焦车和熄焦车。其中装煤车是在焦炉炉顶上由煤塔取煤并往炭化室装煤的焦炉机械,推焦车的作用是完成启闭机械炉门、推焦、平煤等操作,拦焦车的作用是启闭焦侧炉门将炭化室推出的炉饼通过导焦槽导入熄焦车中以完成出焦操作,熄焦车的作用是用以接受炭化室推出的弘叫,并送往熄焦塔通过水喷洒而将其熄灭,然后再把焦炭卸至凉焦台上。
护炉设备是包括炉柱、保护板、纵横拉条、弹簧、炉门框、抵抗墙及机侧、焦侧操作台等。主要作用是利用可调节的弹簧的势能连续不断的向砌体施加足够的、分布均匀合理的保护性压力,使砌体在自身膨胀和外力作用下仍能保持完整性和严密性,并有足够的强度从而保证焦炉的正常生产。
加热煤气供入设备,大型焦炉一般为复热式,可用两种煤气加热,作用是向焦炉输送和调节加压煤气。
荒煤气导出设备包括:上升管、桥管、水封阀、集气管、吸气管、焦油盒以及相应的喷洒氨水系统。其作用为:一是将出炉荒煤气顺利导出,不致因炉门刀边附近煤气压力过高而引起冒烟冒火,但又要保持和控制炭化室在整个结焦过程中为正压;二是将出炉荒煤气适度冷却,不致因温度过高而引起设备变形,阻力声高和鼓风、冷凝的负荷增大,但又要保持焦油和氨水良好的流动性。
4、熄焦、筛焦过程和设备
邯钢焦化厂采用的是湿法熄焦,其熄焦系统包括熄焦塔、喷洒装置、水泵、粉焦沉淀池及粉焦抓钩等。熄焦过程为:熄焦车开进熄焦塔时,利用红外线感受器,接收红焦本身社出的红外线而发出讯号电流,经电流放大触发电路启动熄焦水泵,并借助电子定时装置控制熄焦时间。熄焦时大约有20%的水蒸发,未蒸发的水流入粉焦沉淀池,澄清后的水流入清水池循环利用。熄焦后的焦炭卸至凉焦台上,停放30-40min使其水分蒸发和冷却,个别尚未全部熄灭的红焦,再人工用水补充熄灭。
筛焦按粒度大小将焦炭分为60-80mm、40-60mm、25-40mm、10-25mm、<10mm等级别,主要设备有辊轴筛和共振筛。一般大型焦化厂均设有焦仓和筛焦楼,将大于40mm的焦炭用辊轴筛筛出,经胶带机送往块焦仓。辊轴筛下的焦炭经双层振动筛分成其他三级,分别进入仓库。
七、炼焦化学产品的回收
1、煤气的初冷和焦油的回收
1)荒煤气的主要成分有净焦炉煤气、水蒸气、煤焦油气、苯族烃、氨、萘、硫化氢、其他硫化物、氰化氢等氰化物、吡啶盐等。
回收生产工艺的组成为:焦炉炭化室生成的荒煤气在化学产品回收车间进行冷却、输送、回收煤焦油、氨、硫、苯族烃等化学产品,同时净化煤气。煤气净化车间由冷凝鼓风工段、HPF脱硫工段、硫铵工段、终冷洗苯工段、粗苯蒸馏工段等工段组成,其煤气流程如下:荒煤气→初冷器→电捕焦油器→鼓风机→预冷塔→脱硫塔→喷淋式饱和器→洗终冷塔→洗苯塔→净煤气。
回收炼焦化学产品具有重要的意义。煤在炼焦时,除有75%左右变成焦炭外,还有25%左右生成多种化学产品及煤气。来自焦炉的荒煤气,经冷却和用各种吸收剂处理后,可以提取出煤焦油、氨、萘、硫化氢、氰化氢及粗苯等化学产品,并得到净焦炉煤气,氨可以用于制取硫酸铵和无水氨;煤气中所含的氢可用于制造合成氨、合成甲醇、双氧水、环己烷等,合成氨可进一步制成尿素、硝酸铵和碳酸氢铵等化肥;所含的乙烯可用于制取乙醇和三氯乙烷的原料,硫化氢是生产单斜硫和元素硫的原料,氰化氢可用于制取黄血盐钠或黄血盐钾;粗苯和煤焦油都是很复杂的半成品,经精制加工后,可得到的产品有:二硫化碳、苯、甲苯、三甲苯、古马隆、酚、甲酚和吡啶盐及沥青等,这些产品有广泛的用途,是合成纤维、塑料、染料、合成橡胶、医药、农药、耐辐射材料、耐高温材料以及国防工业的重要原料。
来自焦炉82℃的荒煤气,与焦油和氨水沿吸煤气管道至气夜分离器,气夜分离后荒煤气由上部出来,进入横管式初冷器分两段冷却。上段用循环水,下段用低温水将煤气冷却到21-22℃。由横管式初冷器下部排出的煤气,进入电捕焦油器,除掉煤气中夹带的焦油,再由鼓风机压送至脱硫工段。
由气夜分离器分离下来的焦油和氨水首先进入机械化氨水澄清槽,在此进行氨水、焦油和焦油渣的分离。上部的氨水流入循环氨水中间槽,再由循环氨水泵送到焦炉集气管喷洒冷却煤气,剩余氨水送至剩余氨水槽。澄清槽下部的焦油靠静压流入焦油分离器,进一步进行焦油和焦油渣的沉降分解,焦油用焦油泵送往油库工段焦油贮槽。机械化氨水澄清槽和焦油分离器底部沉降的焦油渣刮至焦油渣车,定期送往煤场,人工掺入炼焦煤中。
进入剩余氨水槽的剩余氨水用剩余氨水泵送入除焦油器,脱除焦油后自流到剩余氨水中间槽,再用剩余氨水中间泵送至硫铵工段剩余蒸氨装置,脱除的焦油自流到地下放空槽。
3)主要设备的构造及工作原理
①离心式鼓风机
离心式鼓风机由导叶轮、外壳和安装在轴上的工作叶轮所组成。煤气由鼓风机吸入后做高速旋转于转子的第一个工作叶轮中心,煤气在离心力的作用下被甩到壳体的环形空隙中心处即产生减压,煤气就不断的被吸入,离开叶轮时煤气很高,当进入环形空隙中,其动压头一部分转变为静压头,煤气的运动减小,并通过导管进入第二个叶轮,产生与第一叶轮相同的作用,煤气的静压头再次被提高。从最后一个叶轮出来的煤气由壳体的环形空隙流入出口连接管被送入压出管路中。
焦化厂所采用的离心式鼓风机按输送量大小分为150m3/min、300 m3/min、750 m3/min 、1200m3/min等多种规格,产生的总压头为30-35kpa。
②横管式初冷器
焦化系统生产中煤气横管式初冷器主要结构是包括初冷器壳体、冷却管管束。横管式初冷器壳体是由钢板焊制而成的直立的长方形器体,壳体的前后两侧是初冷器的管板,管板外装有封头。在壳体侧面上、中部有喷洒液接管,顶部为煤气入口,底部有煤气出口。在横管式初冷器的操作中,除了冷却焦炉煤气外,在冷却器顶部及中部喷洒冷凝液,来吸收焦炉煤气中的萘,并冲刷掉冷却管上沉积的萘,从而有效的提高了传热效率。
③电捕焦油器
电捕焦油器器体是由钢板卷制而成的筒体与器顶封头、器底拱形底组合而成。
电捕焦油器的电场有正电极、负电极组合而成。其正极是又钢管制成,其钢管固定在上下管板上,管板与电捕焦油器筒体焊接而成。电场的负极,装在由绝缘箱垂下杆悬拉的吊架上,其吊杆吊架均有不锈钢制成,吊杆上装着阻力帽以阻止气体冲击绝缘箱。电场负极由不锈钢制成,电晕极板下悬吊着铅坠,以拉直电晕极,电晕极下部由不锈钢制成的下吊架固定位置,电晕极线分别穿入电场沉淀焦油饿正极钢管中心。
2、脱硫工段(HPF脱硫法)
煤气→预冷器→脱硫塔→液封槽→(脱硫液)反应槽→再生塔→泡沫塔→(清夜)反应槽
鼓风机后的煤气进入预冷塔与塔顶喷洒的循环冷却水逆向接触,被冷至30℃,预冷后的煤气进入脱硫塔,与塔顶喷淋下来的脱硫液逆流接触以吸收煤气中的硫化氢(同时吸收煤气中的氨,以补充脱硫液中的碱源)。脱硫后煤气被送入硫铵工段。
吸收了H2S、HCN的脱硫液自流至反应槽,然后用脱硫液泵送入再生塔,同时自再生塔底部通入压缩空气,使溶液在塔内得到氧化再生。再生后的溶液从塔顶经液位调节器自流回脱硫塔循环使用。
浮于再生塔顶部的硫磺泡沫,利用液位差自流入泡沫槽,硫泡沫经泡沫泵送入熔硫釜中,用中压整齐熔硫,清夜流入反应槽,硫磺装袋外销。
为避免脱硫液盐类积累影响脱硫效果,排出少量废液送往配煤。
3、硫铵工段(喷淋式饱和器生产硫铵)
由脱硫及硫回收工段送来的煤气经预热器进入喷淋式硫铵饱和器上段的喷淋室,在此煤气与循环母液充分接触,使其中氨被母液吸收,然后经硫铵饱和器内的除酸器分离酸雾后送至洗脱苯工段。
在饱和器下部的母液,用母液循环泵连续抽出送至上段进行喷洒,吸收煤气中的氨,并循环搅动母液以改善硫铵的结晶过程。饱和器母液中不断有硫铵结晶生成,用结晶泵将其连同一部分母液送入结晶槽沉降,排放到离心机进行离心分离,滤除母液,得到结晶硫铵。离心分离出来的母液与结晶槽溢流出来的母液一同自流回饱和器。从离心机卸出来的硫铵洁净,由螺旋输送机送至沸腾干燥器。沸腾干燥器所需要的热空气是由送风机将空气送入热风器经蒸汽加热后进行沸腾干燥,干燥后的硫铵进入硫铵储槽,然后由包装磅秤称量、包装送入硫铵仓库。
4、终冷洗苯工段
自硫铵工段来的煤气,进入终冷塔分二段用循环冷却水与煤气逆向接触冷却煤气,将煤气冷到一定温度送至洗苯塔。同时,在终冷塔上段加入一定碱液,进一步脱除煤气中的H2S。下段排出的冷凝液送至氰污水处理工段,上段排出的含碱冷凝液送至硫铵工段蒸氨塔顶。
从终冷塔出来的煤气进入洗苯塔,经贫油洗涤脱除煤气中的粗苯后送往各煤气用户。由粗苯蒸馏工段送来的贫油从洗苯塔的顶部喷洒,与煤气逆向接触吸收煤气中的苯,塔底富油经富油泵送至粗苯蒸馏工段脱苯后循环使用。
5、粗苯蒸馏工段
从终冷洗苯装置送来的富油进入富油槽,然后用富油泵依次送经油汽换热器、贫富油换热器,再经管式炉加热后进入脱苯塔,在此用再生器来的直接蒸汽进行汽提和蒸馏。塔顶逸出的粗苯蒸汽经油汽换热器、粗苯冷凝冷却器后,进入油水分离器。分出的粗苯进入粗苯回流槽,部分用粗苯回流泵送至塔顶作为回流液,其余进入粗苯中间槽,再用粗苯产品泵送至油库。
洗煤厂工艺流程
煤炭加工、矸石处理、材料和设备输送等构成了矿井地面系统。其中地面煤炭加工系统由受煤、筛分、破碎、选美、储存、装车等主要环节构成。是矿井地面生产的主体。
受煤是在井口附近设有一定容量的煤仓,接受井下提升到地面的煤炭,保证井口上下均衡连续生产。
筛分
用带孔的筛面把颗粒大小不同的混合物料分成各种粒极的作业叫筛分。晒分所用的机器叫筛分机或者筛子。
在选煤厂中,筛分作业广泛地用于原煤准备和处理上。按照筛分方式不同,分为干法筛分和湿法筛分。
破碎
把大块物料粉碎成小颗粒的过程叫做破碎。用于破碎的机器叫做破碎机。在选煤厂中破碎作业主要有以下要求:
1)适应入选颗粒的要求;精选机械所能处理的煤炭颗粒有一定的范围度,超过这个范围的大块要经过破碎才能洗选。
2)有些煤快是煤与矸石夹杂而生的夹矸煤,为了从中选出精煤,需要破碎成更小的颗粒,使煤和矸煤分离
3)满足用户的颗粒要求,把选后的产品或煤快粉碎到一定的粒度
物料粉碎主要用机械方法,有压碎、劈碎、折断、击碎、磨碎等几种主要方式。
选煤
是利用与其它物质的不同物理、物理-化学性质,在选煤厂内用机械方法去处混在原煤中的杂质,把它分成不同质量、规格的产品,以适应不同有户的需求。
按照选煤厂的位置与煤矿的关选煤厂可以分为:矿井选煤厂、群矿选煤厂、中心选煤厂和用户选煤厂;我国现有的洗煤厂大多是矿井洗煤厂。现代化的洗煤厂是一个由许多作业组成的连续机械加工过程。
跳汰选煤
在垂直脉动的介质中按颗粒密度差别进行选煤过程。跳汰选煤的介质是水或空气,个别的也用悬浮液。选煤中以水力跳汰的最多。
跳汰机是利用跳汰分选原理将入选原料按密度大小分选为精煤、中煤和矸煤等产品设备。
重介选煤
在密度大于1g/cm的介质中,按颗粒密度的的大小差异进行选煤,叫做重介质选煤或重介选煤。选煤所用的重介质有重液和重选浮液两类。重介选煤的主要优点是分选效率高与其它选煤方法;入选力度范围宽,分选机入料粒为1000-6mm,漩流器为80-0.15mm生产控制易于自动化。重介选煤的缺点是生产工艺复杂,生产费用高,设备磨损快,维修量大。
重介选煤一般都分级入选。分选块煤一般在重力作用下用重介质分选机进行;分选沫煤在离心力作用下用重介质漩流器进行。
存储
装车:包括装车(船)、吊车和计量。
煤制甲醇工艺
气化
a)煤浆制备
由煤运系统送来的原料煤干基(<25mm)或焦送至煤贮斗,经称重给料机控制输送量送入棒磨机,加入一定量的水,物料在棒磨机中进行湿法磨煤。为了控制煤浆粘度及保持煤浆的稳定性加入添加剂,为了调整煤浆的PH值,加入碱液。出棒磨机的煤浆浓度约65%,排入磨煤机出口槽,经出口槽泵加压后送至气化工段煤浆槽。煤浆制备首先要将煤焦磨细,再制备成约65%的煤浆。磨煤采用湿法,可防止粉尘飞扬,环境好。用于煤浆气化的磨机现在有两种,棒磨机与球磨机;棒磨机与球磨机相比,棒磨机磨出的煤浆粒度均匀,筛下物少。煤浆制备能力需和气化炉相匹配,本项目拟选用三台棒磨机,单台磨机处理干煤量43~53t/h,可满足60万t/a甲醇的需要。
为了降低煤浆粘度,使煤浆具有良好的流动性,需加入添加剂,初步选择木质磺酸类添加剂。
煤浆气化需调整浆的PH值在6~8,可用稀氨水或碱液,稀氨水易挥发出氨,氨气对人体有害,污染空气,故本项目拟采用碱液调整煤浆的PH值,碱液初步采用42%的浓度。
为了节约水源,净化排出的含少量甲醇的废水及甲醇精馏废水均可作为磨浆水。
b)气化
在本工段,煤浆与氧进行部分氧化反应制得粗合成气。
煤浆由煤浆槽经煤浆加压泵加压后连同空分送来的高压氧通过烧咀进入气化炉,在气化炉中煤浆与氧发生如下主要反应:
CmHnSr+m/2O2—→mCO+(n/2-r)H2+rH2S
CO+H2O—→H2+CO2
反应在6.5MPa(G)、1350~1400℃下进行。
气化反应在气化炉反应段瞬间完成,生成CO、H2、CO2、H2O和少量CH4、H2S等气体。
离开气化炉反应段的热气体和熔渣进入激冷室水浴,被水淬冷后温度降低并被水蒸汽饱和后出气化炉;气体经文丘里洗涤器、碳洗塔洗涤除尘冷却后送至变换工段。
气化炉反应中生成的熔渣进入激冷室水浴后被分离出来,排入锁斗,定时排入渣池,由扒渣机捞出后装车外运。
气化炉及碳洗塔等排出的洗涤水(称为黑水)送往灰水处理。
c)灰水处理
本工段将气化来的黑水进行渣水分离,处理后的水循环使用。
从气化炉和碳洗塔排出的高温黑水分别进入各自的高压闪蒸器,经高压闪蒸浓缩后的黑水混合,经低压、两级真空闪蒸被浓缩后进入澄清槽,水中加入絮凝剂使其加速沉淀。澄清槽底部的细渣浆经泵抽出送往过滤机给料槽,经由过滤机给料泵加压后送至真空过滤机脱水,渣饼由汽车拉出厂外。
闪蒸出的高压气体经过灰水加热器回收热量之后,通过气液分离器分离掉冷凝液,然后进入变换工段汽提塔。
闪蒸出的低压气体直接送至洗涤塔给料槽,澄清槽上部清水溢流至灰水槽,由灰水泵分别送至洗涤塔给料槽、气化锁斗、磨煤水槽,少量灰水作为废水排往废水处理。
洗涤塔给料槽的水经给料泵加压后与高压闪蒸器排出的高温气体换热后送碳洗塔循环使用。
2)变换
在本工段将气体中的CO部分变换成H2。
本工段的化学反应为变换反应,以下列方程式表示:
CO+H2O—→H2+CO2
由气化碳洗塔来的粗水煤气经气液分离器分离掉气体夹带的水分后,进入气体过滤器除去杂质,然后分成两股,一部分(约为54%)进入原料气预热器与变换气换热至305℃左右进入变换炉,与自身携带的水蒸汽在耐硫变换催化剂作用下进行变换反应,出变换炉的高温气体经蒸汽过热器与甲醇合成及变换副产的中压蒸汽换热、过热中压蒸汽,自身温度降低后在原料气预热器与进变换的粗水煤气换热,温度约335℃进入中压蒸汽发生器,副产4.0MPa蒸汽,温度降至270℃之后,进入低压蒸汽发生器温度降至180℃,然后进入脱盐水加热器、水冷却器最终冷却到40℃进入低温甲醇洗1#吸收系统。
另一部分未变换的粗水煤气,进入低压蒸汽发生器使温度降至180℃,副产0.7MPa的低压蒸汽,然后进入脱盐水加热器回收热量,最后在水冷却器用水冷却至40℃,送入低温甲醇洗2#吸收系统。
气液分离器分离出来的高温工艺冷凝液送气化工段碳洗塔。
气液分离器分离出来的低温冷凝液经汽提塔用高压闪蒸气和中压蒸汽汽提出溶解在水中的CO2、H2S、NH3后送洗涤塔给料罐回收利用;汽提产生的酸性气体送往火炬。
3)低温甲醇洗
本工段采用低温甲醇洗工艺脱除变换气中CO2、全部硫化物、其它杂质和H2O。
a)吸收系统
本装置拟采用两套吸收系统,分别处理变换气和未变换气,经过甲醇吸收净化后的变换气和未变换气混合,作为甲醇合成的新鲜气。
由变换来的变换气进入原料气一级冷却器、氨冷器、进入分离器,出分离器的变换气与循环高压闪蒸气混合后,喷入少量甲醇,以防止变换气中水蒸气冷却后结冰,然后进入原料气二级冷却器冷却至-20℃,进入变换气甲醇吸收塔,依次脱除H2S+COS、CO2后在-49℃出吸收塔,然后经二级原料气冷却器,一级原料气冷却器复热后去甲醇合成单元。净化气中CO2含量约3.4%,H2S+COS<0.1PPm。
来自甲醇再生塔经冷却的甲醇-49℃从甲醇吸收塔顶进入,吸收塔上段为CO2吸收段,甲醇液自上而下与气体逆流接触,脱除气体中CO2,CO2的指标由甲醇循环量来控制。中间二次引出甲醇液用氨冷器冷却以降低由于溶解热造成的温升。在吸收塔下段,引出的甲醇液大部分进入高压闪蒸器;另一部分溶液经氨冷器冷却后回流进入H2S吸收段以吸收变换气中的H2S和COS,自塔底出来的含硫富液进入H2S浓缩塔。为减少H2和CO损失,从高压闪蒸槽闪蒸出的气体加压后送至变换气二级冷却器前与变换气混合,以回收H2和CO。
未变换气的吸收流程同变换气的吸收流程。
b)溶液再生系统
未变换气和变换气溶液再生系统共用一套装置。
从高压闪蒸器上部和底部分别产生的无硫甲醇富液和含硫甲醇富液进入H2S浓缩塔,进行闪蒸汽提。甲醇富液采用低压氮气汽提。高压闪蒸器上部的无硫甲醇富液不含H2S从塔上部进入,在塔顶部降压膨胀。高压闪蒸器下部的含硫甲醇富液从塔中部进入,塔底加入的氮气将CO2汽提出塔顶,然后经气提氮气冷却器回收冷量后,作为尾气高点放空。
富H2S甲醇液自H2S浓缩塔底出来后进热再生塔给料泵加压,甲醇贫液冷却器换热升温进甲醇再生塔顶部。甲醇中残存的CO2以及溶解的H2S由再沸器提供的热量进行热再生,混和气出塔顶经多级冷却分离,甲醇一级冷凝液回流,二级冷凝液经换热进入H2S浓缩塔底部。分离出的酸性气体去硫回收装置。
从原料气分离器和甲醇再生塔底出来的甲醇水溶液经泵加压后甲醇水分离器,通过蒸馏分离甲醇和水。甲醇水分离器由再沸器提供。塔顶出来的气体送到甲醇再生塔中部。塔底出来的甲醇含量小于100PPm的废水送水煤浆制备工序或去全厂污水处理系统。
c)氨压缩制冷
从净化各制冷点蒸发后的-33℃气氨气体进入氨液分离器,将气体中的液粒分离出来后进入离心式制冷压缩机一段进口压缩至冷凝温度对应的冷凝压力,然后进入氨冷凝器。气氨通过对冷却水放热冷凝成液体后,靠重力排入液氨贮槽。液氨通过分配器送往各制冷设备。
4)甲醇合成及精馏
a)甲醇合成
经甲醇洗脱硫脱碳净化后的产生合成气压力约为5.6MPa,与甲醇合成循环气混合,经甲醇合成循环气压缩机增压至6.5MPa,然后进入冷管式反应器(气冷反应器)冷管预热到235℃,进入管壳式反应器(水冷反应器)进行甲醇合成,CO、CO2和H2在Cu-Zn催化剂作用下,合成粗甲醇,出管壳式反应器的反应气温度约为240℃,然后进入气冷反应器壳侧继续进行甲醇合成反应,同时预热冷管内的工艺气体,气冷反应器壳侧气体出口温度为250℃,再经低压蒸汽发生器,锅炉给水加热器、空气冷却器、水冷器冷却后到40℃,进入甲醇分离器,从分离器上部出来的未反应气体进入循环气压缩机压缩,返回到甲醇合成回路。
一部分循环气作为弛放气排出系统以调节合成循环圈内的惰性气体含量,合成弛放气送至膜回收装置,回收氢气,产生的富氢气经压缩机压缩后作为甲醇合成原料气;膜回收尾气送至甲醇蒸汽加热炉过热甲醇合成反应器副产的中压饱和蒸汽(2.5MPa),将中压蒸汽过热到400℃。
粗甲醇从甲醇分离器底部排出,经甲醇膨胀槽减压释放出溶解气后送往甲醇精馏工段。
系统弛放气及甲醇膨胀槽产生的膨胀气混合送往工厂锅炉燃料系统。
甲醇合成水冷反应器副产中压蒸汽经变换过热后送工厂中压蒸汽管网。
b)甲醇精馏
从甲醇合成膨胀槽来的粗甲醇进入精馏系统。精馏系统由预精馏塔、加压塔、常压塔组成。预精馏塔塔底出来的富甲醇液经加压至0.8MPa、80℃,进入加压塔下部,加压塔塔顶气体经冷凝后,一部分作为回流,一部分作为产品甲醇送入贮存系统。由加压塔底出来的甲醇溶液自流入常压塔下塔进一步蒸馏,常压塔顶出来的回流液一部分回流,一部分作为精甲醇经泵送入贮存系统。常压塔底的含甲醇的废水送入磨煤工段作为磨煤用水。在常压塔下部设有侧线采出,采出甲醇、乙醇和水的混合物,由汽提塔进料泵送入汽提塔,汽提塔塔顶液体产品部分回流,其余部分作为产品送至精甲醇中间槽或送至粗甲醇贮槽。汽提塔下部设有侧线采出,采出部分异丁基油和少量乙醇,混合进入异丁基油贮槽。汽提塔塔底排出的废水,含少量甲醇,进入沉淀池,分离出杂醇和水,废水由废水泵送至废水处理装置。
c)中间罐区
甲醇精馏工序临时停车时,甲醇合成工序生产的粗甲醇,进入粗甲醇贮罐中贮存。甲醇精馏工序恢复生产时,粗甲醇经粗甲醇泵升压后送往甲醇精馏工序。
甲醇精馏工序生产的精甲醇,进入甲醇计量罐中。经检验合格的精甲醇用精甲醇泵升压送往成品罐区甲醇贮罐中贮存待售。
5)空分装置
本装置工艺为分子筛净化空气、空气增压、氧气和氮气内压缩流程,带中压空气增压透平膨胀机,采用规整填料分馏塔,全精馏制氩工艺。
原料空气自吸入口吸入,经自洁式空气过滤器除去灰尘及其它机械杂质。过滤后的空气进入离心式空压机经压缩机压缩到约0.57MPa(A),然后进入空气冷却塔冷却。冷却水为经水冷塔冷却后的水。空气自下而上穿过空气冷却塔,在冷却的同时,又得到清洗。
经空冷塔冷却后的空气进入切换使用的分子筛纯化器空气中的二氧化碳、碳氢化合物和水分被吸附。分子筛纯化器为两只切换使用,其中一只工作时,另一只再生。纯化器的切换周期约为4小时,定时自动切换。
净化后的空气抽出一小部分,作为仪表空气和工厂空气。
其余空气分成两股,一股直接进入低压板式换热器,从换热器底部抽出后进入下塔。另外一股进入空气增压机。
经过空气增压机的中压空气分成两部分,一部分进入高压板式换热器,冷却后进入低温膨胀机,膨胀后空气进入下塔精馏。另一部分中压空气经过空气增压机二段压缩为高压空气,进入高压板式换热器,冷却后经节流阀节流后进入下塔。
空气经下塔初步精馏后,获得富氧液空、低纯液氮、低压氮气,其中富氧液空和低纯液氮经过冷器过冷后节流进入上塔。经上塔进一步精馏后,在上塔底部获得液氧,并经液氧泵压缩后进入高压板式换热器,复热后出冷箱,进入氧气管网。
在下塔顶部抽取的低压氮气,进入高压板式换热器,复热后送至全厂低压氮气管网。
从上塔上部引出污氮气经过冷器、低压板式换热器和高压板式换热器复热出冷箱后分成两部分:一部分进入分子筛系统的蒸汽加热器,作为分子筛再生气体,其余污氮气去水冷塔。
从上塔中部抽取一定量的氩馏份送入粗氩塔,粗氩塔在结构上分为两段,第二段氩塔底部的回流液经液体泵送入第一段顶部作为回流液,经粗氩塔精馏得到99.6Ar,2ppmO2的粗氩,送入精氩塔中部,经精氩塔精馏在精氩塔底部得到纯度为99.999%Ar的**氩作为产品抽出送入进贮槽。
今天的内容先分享到这里了,读完本文《煤制甲醇的工艺流程?》之后,是否是您想找的答案呢?想要了解更多,敬请关注www.zuqiumeng.cn,您的关注是给小编最大的鼓励。
本文来自网络,不代表本站立场,转载请注明出处:https://www.zuqiumeng.cn/wenda/215736.html