重庆甲醇水泵推荐
今天运困体育就给我们广大朋友来聊聊陕西甲醇水泵推荐,希望能帮助到您找到想要的答案。
烧甲醇损害油泵么?
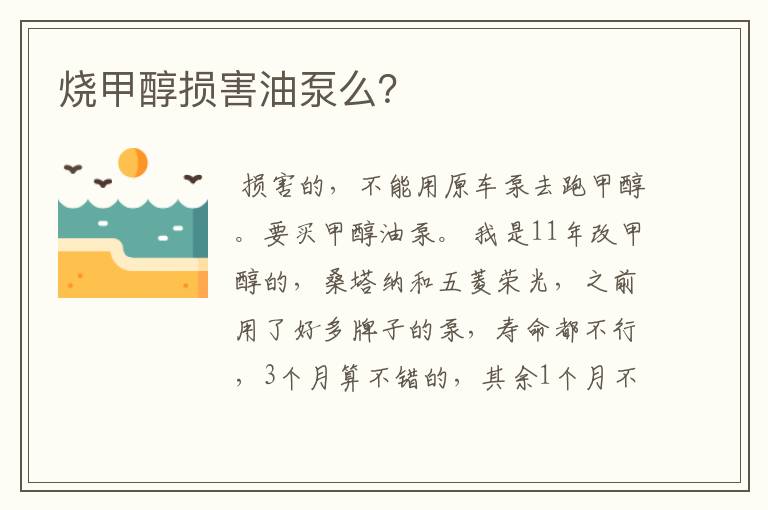
损害的,不能用原车泵去跑甲醇。要买甲醇油泵。
我是11年改甲醇的,桑塔纳和五菱荣光,之前用了好多牌子的泵,寿命都不行,3个月算不错的,其余1个月不到就坏了。后来网上买了个 9v甲醇泵,蛮好的,12年装的 用到了现在,和我一起改甲醇的朋友我很多都推荐了这个。淘宝买的,9v甲醇泵,可以自己去搜搜看。
化学药剂泵常用水泵材质有哪些?
美宝化学药剂泵是用于输送强弱酸碱介质、强氧化物、有机溶质、腐蚀性介质的水泵。
1:化学药剂泵输送的化学药剂一般有浓度硫酸(含硫化物)、盐酸(次氯酸)、硝酸、铬酸、氢氟酸、磷酸、次氯酸钠、醋酸、草酸、乳酸、氨水、海水、甲醇、苯酚等酸碱介质。
2:化学药剂泵主要用于输送、提升、循环、卸料、卸车、加药等,具有耐酸碱泵,耐腐蚀、无泄漏特点。
3:化学药剂泵的材质有PP、PVDF、FRPP、不锈钢、氟塑料等。一般常温选FRPP材质,高温选用PVDF材质。对于高温高浓度或含有其它腐蚀介质等苛刻要求时,可选用316不锈钢或氟塑料泵。可根据具体使用工艺来选择。
4:在选择用化学药剂泵时,会根据现场工况、扬程、流量来选型。
重庆水泵厂有限责任公司对于煤化工中的贫甲醇泵有些什么特点?
一. 高压自平衡离心泵技术特点及优势
1.高压自平衡离心泵概述
重庆水泵厂有限责任公司于1983年开始研制、开发、生产SD型筒体式双壳体高压自平衡离心泵,1985开始生产,于1987年成功运行于武钢集团高压除鳞系统,之后形成系列化产品,现有500多种规格,最大流量1000m3/h,最高扬程3500m,可输送含固、含气的二相流和三相流介质,介质温度范围-110℃~400℃。
为了满足市场不断发展、变化的需求,于上世纪90年代末,公司在SD系列筒体式双壳体高压自平衡离心泵的基础上发展了ZD系列——单壳体高压自平衡离心泵,包括节段式和双蜗壳轴向剖分式两种结构。
在研发SD、ZD系列高压自平衡离心泵的过程中,公司致力于自主创新,同时吸收、消化国外先进技术;该系列泵拥有自主知识产权,现拥有五项国家专利技术,获得中国机械工业科学技术奖。
根据离心泵轴向力产生机理,SD、ZD系列泵的叶轮采用对称布置形式,科学巧妙地实现了轴向力自平衡(不需设计平衡盘、平衡鼓),完全避免了转子部件与壳体部件的接触,突破了传统多级泵的结构瓶颈,拓展了泵的运行工况条件,适用于交变工况、含固体颗粒及溶气的低有效汽蚀余量等特殊工况。
压差是形成泄漏的基本条件;传统多级泵设计口环、轴套等进行节流密封,必然有泄漏并且容易磨损;SD、ZD系列泵的叶轮级间和轴端均采用无接触多头反抽螺旋密封,螺旋反抽产生“泵送作用”,形成封力,逐渐升压,避免了泄漏及磨损,提高了泵的容积效率及抗气蚀性能。
SD、ZD系列泵的轴端在螺旋密封外面还设计了机械密封(或干气密封或填料密封或泥状填料密封或梳齿密封),在运转中起辅助密封作用,同时保证停车时介质不泄漏,由于螺旋密封对固体颗粒有包容性及反抽输送特点,固体颗粒到达不了机封,机封寿命大为提高。
SD系列泵的芯包分节段型多导叶式和双蜗壳轴向剖分式,芯包可设计为整体抽出式,在不动所有连接管路的情况下快速换修芯包。
SD、ZD系列泵以其技术先进、性价比高等优势得到广大用户的青睐,广泛应用于高压井注水、原油外输、钢厂除鳞以及炼油化工、煤化工、热电、核工业等领域输送大流量、高扬程的各种介质,良好的密封性能更加适合输送各种腐蚀性、磨蚀性、易燃、易爆有毒介质及低有效气蚀余量工况。
2.平衡盘结构多级离心泵的使用工况局限性
2.1轴向力平衡机理
叶轮同向结构多级离心泵的轴向力是所有单级叶轮产生轴向力的总和,由平衡盘机构产生反向力平衡叶轮轴向力。
以流量300m3/h,单级扬程135m计算,单级叶轮产生的轴向力为2500kgf。
2.2 受限于交变工况
泵在稳定运行工况条件下,多级叶轮产生的巨大轴向力由平衡盘机构平衡。
当运行工况在小范围内变化时,由于叶轮产生的轴向力发生瞬间变化,转子部件突然窜动,改变了平衡环与平衡盘之间的间隙以平衡轴向力,直到新的平衡建立后转子部件才停止窜动(轴向串量为3~5mm)。
在泵启动、停止及工况陡变时,产生的巨大轴向力由平衡盘与平衡环直接接触承担,平衡环与旋转的平衡盘摩擦容易发生干烧现象和咬死现象,严重时扭断主轴。
因此,平衡盘结构多级离心泵在交变工况运行条件下,易发生故障和事故,难以保证泵的可靠运行和使用寿命。
2.3 受限于输送含有固体颗粒的介质
高压介质进入平衡机构节流面后,高速流动,形成冲刷,固体颗粒必然加快磨蚀平衡盘和平衡环;在平衡盘和平衡环直接接触的情况下,固体颗粒对平衡机构造成最大破坏,容易出现咬死及断轴的现象。
2.4 受限于输送溶有气体的介质
平衡环与平衡盘之间是间隙节流形式,节流后压力下降到平衡水管的压力(即泵进口压力),泄漏的介质喷射而出在平衡盘的背面形成旋涡区,压力进一步降低,溶气介质易逸出气泡,泵产生汽蚀。
3.轴向力自平衡结构多级离心泵的技术优势
3.1 轴向力平衡机理
采用叶轮对称布置形式,在运转中叶轮产生的轴向力相互抵消,实现轴向力自平衡;当叶轮级数为奇数时,首级叶轮采用双吸入形式(或在高压进水端第一级设计平衡套)。
该新技术我公司已获得国家专利,专利证书号:ZL 03 2 35051.1。
3.2 技术优势
没有平衡盘(鼓)结构,叶轮对称布置,轴向力自平衡,泵的可靠性更高,无易损件。
适用工况更广,适合于交变工况使用条件,适合于输送含固体颗粒的介质,适合于输送溶气的介质;避免了平衡盘结构多级离心泵输送含固、气、液三相流介质时,平衡机构发生的汽蚀、磨蚀等现象;大大提高泵组的无故障运行周期。
3.3 残余轴向力的平衡
由于叶轮的加工误差,轴向力自平衡结构多级离心泵在运转中会产生残余轴向力;在任何情况下,最大残余轴向力不超过单个叶轮产生的轴向力的一半。
残余轴向力,由泵非驱动端设置的自动找正推力系统——双面推力轴承(或双列圆锥滚子推力轴承)来承担。
3.4 转子部件串量小
由于轴向力自平衡多级离心泵的残余轴向力小,由推力轴承承担,因此转子部件串量小,运行平稳。(采用双面推力轴承, 串量为0.35~0.4mm;采用双列圆锥滚子推力轴承, 串量为0.1~0.2mm)
4.采用节流密封的多级离心泵的使用局限性
4.1 由于有泄漏降低效率
多级离心泵的每一级叶轮都对介质进行增压,叶轮级间存在单级扬程的压差,有压差必然有泄漏及磨损,一般采用口环节流以减少泄漏、降低磨损;节流面间隙的大小决定泄漏量的多少,泄漏必然降低容积效率,从而影响泵的效率;介质中如有固体颗粒必然加速磨蚀节流口环,甚至出现卡死、烧死现象。
4.2 受限于输送含固体颗粒介质
在轴的两端一般采用轴套节流后再加机封(或填料密封),随着轴套的磨损让机封承受压力逐渐加大,介质中如有固体颗粒会沿着节流间隙到达机封处,迅速磨损机封动、静环,让机封很快失效。
4.3 受限于输送溶气介质
在首级叶轮处由于采用口环节流,节流后压力下降到泵进口压力,泄漏的介质喷射而出形成旋涡区,压力进一步降低,溶气介质易逸出气泡,泵产生汽蚀。
5.采用螺旋反抽密封的多级离心泵的技术优势
5.1 螺旋反抽密封原理
在转子部件上的密封部位设计多头螺旋,高速旋转的螺旋产生“泵送作用”,给介质一个反抽力;反抽力略大于介质向低压侧泄漏的压差,从而阻止介质泄漏,实现无接触螺旋反抽密封。
螺旋反抽的密封力由螺旋的头数(一般选6~12头)、升角、导程、转速及与密封套的间隙等共同决定。在设计中必须经过精确计算,并根据多次试验数据及实践经验数据进行优化设计。
该新技术我公司已获得国家专利,专利证书号:ZL 03 235052.X。
5.2 技术优势
叶轮密封采用多头无接触螺旋反抽密封,介质不泄漏,提高泵的容积效率,从而提高泵的效率,也避免了溶气介质逸出气泡,提高泵的汽蚀性能;螺旋对固体颗粒有包容性及反抽输送的特点,提高泵密封的使用寿命。
轴端的第一级密封采用多头无接触螺旋反抽密封,在运转中对介质进行完全密封,保证密封的可靠性;轴端的第二级密封采用机械密封(或填料密封、干气密封等)保证停车时不泄漏,在运转中起辅助密封作用;由于固体颗粒到达不了机封的密封面,对输送含固体颗粒的介质,机械密封的寿命从根本上得到了保证。
采用螺旋反抽的多级离心泵效率高、密封可靠、易损件寿命长、适用工况更广,适合于输送含固体颗粒的介质,适合于输送溶气的介质,适合于输送易燃、易爆、有毒有害等特殊介质。
6.高压自平衡多级离心泵主要特点
6.1叶轮及轴
轴的内曲面与叶轮盖共同形成叶轮进口流道,改善了叶轮的吸入性能及流体运动特性,同时将转子部件的径向尺寸减小。
叶轮5级;首级叶轮采用对称双吸入结构,产生的轴向力自平衡,同时增大了叶轮的进口流道面积,改善了气蚀性能,保证NPSHr≤7m;其余4级完全对称布置,产生的轴向力自平衡;运转中轴向力是自平衡的,不需要传统多级离心泵设置专门的轴向力平衡机构(如平衡盘、平衡鼓等)。
6.2外壳体及密封
外壳体部件为整体制造,与泵盖形成的高压区只有左右两个高压静密封面,保证了泵整体密封的可靠性,避免了节段式多级离心泵(BB4结构)存在多个高压密封面、拉杆较长、不可靠的局限性,也避免了单壳体水平剖分多级离心泵(BB3结构)的密封面过大密封不可靠的局限性。
外壳体的双面高压静密封采用过定位密封的专利技术,密封材料为金属缠绕垫,确保密封可靠。
内壳体带转子为整体抽芯式,可实现4小时内整体更换。
外壳完全承担因与外部管路连接带来的力、力矩及热冲击等,保证了内壳体及转子部件不受外力而变形,大大提高了泵的可靠性,确保了泵无故障运行周期。
6.3内壳体及密封
内壳体为轴向剖分式。
采用180°完全对称布置的蜗壳流道,径向力自平衡,减小轴的挠度提高了轴的刚性。
双蜗室的设计比径向导叶式及单蜗壳结构的效率至少提高1%。
运转时内壳体与外壳体间的高压将内壳体压紧,因此越受压密封效果越好,密封越可靠。水平剖分面采用整体精磨技术,装配时涂上密封胶,用四周布置的螺栓压紧。
6.4级间密封
由于甲醇的粘度比水还低,流动性好,穿透力强,因此我公司的多级泵叶轮级间密封采用的多头螺旋反抽形式的优势在这里得到了很好的体现,提高容积效率。
在内壳体中部高低分界处,叶轮的背面均设计了较长的多头反抽螺旋,保证总的反抽力大于等于压差。
在转子部件中间设置自润滑轴承支承,减小轴的动挠度,使转子部件运行在第一临界转速以内运转。
6.5轴端密封
进水段轴端、高压进水段的轴端根据最大压差设计了多头螺旋反抽密封机构,运转中多头螺旋能保证完全密封,螺旋密封外腔室用导流管与低压进水段相连接,因此运转中两端的机械密封承担负荷是一样的。
今天的内容先分享到这里了,读完本文《重庆甲醇水泵推荐》之后,是否是您想找的答案呢?想要了解更多,敬请关注www.zuqiumeng.cn,您的关注是给小编最大的鼓励。
本文来自网络,不代表本站立场,转载请注明出处:https://www.zuqiumeng.cn/wenda/242669.html