广西钢衬四氟气液分离器 广西甲烷压缩机气液分离器
今天运困体育就给我们广大朋友来聊聊广西甲烷压缩机气液分离器,希望能帮助到您找到想要的答案。
压缩机氨液分离器的操作是怎样的?
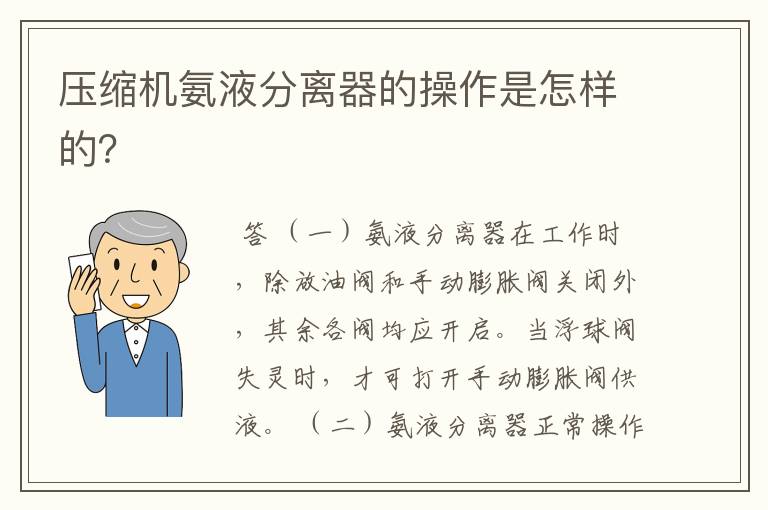
答(一)氨液分离器在工作时,除放油阀和手动膨胀阀关闭外,其余各阀均应开启。当浮球阀失灵时,才可打开手动膨胀阀供液。 (二)氨液分离器正常操作是控制好液面高度,金属管液面指示器1/2处应有霜层。 (三)根据压缩机的吸气温度、金属管液面指示器和冷却排管结霜情况判断供液量是否合适。要求既能满足冷库降温要求,又不致于造成压缩机发生湿冲程。
氨液分离器的介绍
答氨液分离器,是将氨液与氨气分离开,部分将回到蒸发器内,断续工作吸热,至使气体给螺杆压缩机吸收进行挤压。氨液分离器是将蒸发器所蒸发的汽体在被吸入压缩机前,分离出其中含有的氨液,防止氨液进入压缩机产生湿行程和液击现象;此外,还用以分离节流而产生的汽体,提高蒸发器的有效传热面积,稳定重力供液液面。气液分离器的筒体直径按氨气流速不大于0.5m/s选定。
有什么常用的软化水处理方法?
答本发明公开了一种高效自发结晶的电化学脱盐软化水处理方法,将电解槽分隔成阳极室和阴极室,并分别置有阳极板和阴极板;根据I≥1.01Qη(M+2M2)得到电流,待软化的水流经阴极室,通电后,在阴极室内形成强碱性区域,体系pH≥10,产生的OH‑,使Ca2+生成CaCO3晶体,Mg2+生成Mg(OH)2晶体,且随着pH值的增大,碳酸钙晶体的zeta电位降低,晶体聚团行为加强而讯速形成晶核;过饱和的晶体悬浮液随水流流出电解室的过程中,以此晶核为生长点并迅速成长,实现自发结晶,再进行沉降或过滤,即完成软化。本发明计算出适宜电流值,将水中钙镁离子一次性除去,且在处理过程中阴极板上几乎不会附着水垢,电能利用效率高达90%,极大提高了设备的处理能力和便于实现数字化和自动化控制。
权利要求书
1.一种高效自发结晶的电化学脱盐软化水处理方法,其特征在于,包括以下步骤:
(1)通过隔膜或细孔板将电解槽分隔成阳极室和阴极室,并将阳极板和阴极板分别置于阳极室和阴极室中;
(2)通一电流,所述的电流根据I≥1.01Qη(M+2M2)计算得到,其中,I为电极板的电流,单位:A;η为目标软化率,单位:1;Q为阴极室的水流量,单位:L/s;当M0>M1时,M=M0;当M0[(M0+M2)/(M1+M2)]时,M=2M1-M0;M0为待软化水的碱度,单位:mgCaCO3/L;M1为待软化水的钙硬度,单位:mgCaCO3/L;M2为待软化水的镁硬度,单位:mgCaCO3/L;
(3)待软化的水流经阴极室,通电后,在阴极室内形成强碱性区域,体系pH≥10,电解产生的OH-,与HCO3-反应生成CO32-,然后与水体中的Ca2+结合生成CaCO3晶体;与Mg2+结合生成Mg(OH)2晶体,且随电解的继续,阴极液pH值增大,CaCO3晶体的zeta电位降低,晶体聚团行为加强而迅速形成晶核,随高速水流流出阴极室的过饱和CaCO3和Mg(OH)2悬浮液以此晶核为生长点并迅速成长,实现自发结晶,生成肉眼可见的固体颗粒物,悬浮于水中,再进行沉降或过滤,即完成软化。
2.根据权利要求1所述的高效自发结晶的电化学脱盐软化水处理方法,其特征在于,还包括在M0[(M0+M2)/(M1+M2)]时,向阴极液中通入足量空气或二氧化碳。
3.根据权利要求2所述的高效自发结晶的电化学脱盐软化水处理方法,其特征在于,常温常压下通入空气的流量根据Q1=0.61Q(M1-M0)计算得到,其中,Q1为向阴极室通入空气的流量,单位:L/s。
4.根据权利要求2所述的高效自发结晶的电化学脱盐软化水处理方法,其特征在于,常温常压下通入CO2的流量根据Q0=2.45Q(M1-M0)·10-4计算得到,其中,Q0为向阴极室通入CO2的流量,单位:L/s。
5.根据权利要求1所述的高效自发结晶的电化学脱盐软化水处理方法,其特征在于,所述的阳极板为碳电极、贵金属电极或钛基金属氧化物电极中的一种;所述的阴极板为定型导电材料中的一种。
6.根据权利要求1所述的高效自发结晶的电化学脱盐软化水处理方法,其特征在于,所述的隔膜为阴离子交换膜、阳离子交换膜、双极膜、石棉纤维膜、无纺布、化纤滤布或陶瓷隔膜中的一种;所述的细孔隔板为带有微小细孔且不影响导电的塑料薄板。
7.一种利用权利要求1~6所述的高效自发结晶的电化学脱盐软化水处理方法软化硬水的装置。
8.根据权利要求7所述的软化硬水的装置,其特征在于,至少在所述的阴极室的两端分别设有进水口和出水口,在所述的进水口上设有空气或二氧化碳补气口,在所述的出水口上连有过滤器或沉降池。
9.根据权利要求8所述的软化硬水的装置,其特征在于,在所述的出水口与所述的过滤器或沉降池之间设有第一气液分离器。
10.一种软化硬水的系统,其特征在于,将若干个权利要求8所述的电解槽并联、串联或串并复合连接,且在阴极室出水口的汇集处设有第二气液分离器。
说明书
一种高效自发结晶的电化学脱盐软化水处理方法及其装置
技术领域
本发明属于电化学软化水技术领域,特别涉及一种高效自发结晶的电化学脱盐软化水处理方法及其装置。
背景技术
利用电化学技术进行水体脱盐除垢处理,早在2006年就有文献(Desalination,2006,201:150)报道,随后也有不少国内文献及专利(西安交通大学学报,2009,43(5):104;专利公开CN105523611A、CN204198498U)报道过,并在工程实践中得到一定程度的应用。相比于传统的消石灰软化法,电化学脱盐软化水技术占地空间小、处理快、不需要使用絮凝剂无二次污染、废弃固体物少,操作简单方便,可实现数字化控制,具有很高的经济效益和环境效益。用于冷却循环水的除垢防垢领域,与以往传统的化学加药方法以及电磁技术、超声波技术相比,电化学技术的优点在于能够将水中的成垢的钙镁离子以水垢沉积的方式从水中取出,并能提高浓缩倍数,达到节水减排的目的。
现有的电化学设备主要用于冷却循环水的除垢防垢领域,为提高除垢效率,中国专利公开CN105621538A、CN201923867U及CN105329985A等专利对电化学除垢设备进行了相应的优化设计,其创新点在于充分优化电化学设备内部结构,扩大阴极面积,简化操作,提高设备的处理效率与处理能力。
为了摆脱极板面积大小的限制因素,以色列文献(Desalination,2010,263:285;Journal of Membrance Science,2013,445:88)提出了一种新的处理方法,利用阳离子交换膜将电解槽分隔为阳极室与阴极室,将待处理的水流经阴极室后,引入外部结晶器内进行诱发结晶以提高极板处理能力,电能利用率达到50%。中国专利CN204198498U利用刮刀刮掉阴极板垢以提供微小晶核增加结晶比表面积,虽在一定程度上提高了电能的利用率,但其电能利用率依旧偏低,一是增加了阴极动力旋转部分的电耗,二是由于其辅助电极接正电且在阴极室内,其表面必定会析氧(氯)而产生H+,可消耗阴极产生的部分OH-而导致电能利用率降低,另外其在后续工艺中提及需添加絮凝剂造成二次污染及处理成本的增加,另外其设备内腔底部没有隔膜将阴阳两室分开,而其实施例中阳极室酸性水一直往复循环部分H+必会进入阴极室,也会降低电能的利用率。生活中大部分水体都是硬水即碱度小于硬度(等同于重碳酸根的含量低于钙镁量),故在不补加二氧化碳的情况下不能完全消除硬度。专利CN106277369A虽也提及阴阳极间加隔膜,但同样要求阴极室出水口需连接一外部结晶器诱发结晶,结晶器体积庞大且时效性低,因无二氧化碳的补给同样存在硬度水条件下不能完全消除硬度达到彻底软化水的目的。
发明内容
本发明的第一目的是提供了一种高效自发结晶的电化学脱盐软化水处理方法,向电解槽中通入电流,使得阴极室内形成强碱性区域,利用电解产生的OH-,使得Ca2+生成CaCO3晶体,与Mg2+生成Mg(OH)2晶体,并随着电解的进行,阴极室pH值增大,碳酸钙晶体聚团行为加强而迅速形成晶核,使得过饱和的CaCO3和Mg(OH)2悬浮液高效自发结晶,避免了诱发结晶和外加絮凝剂而带来的二次污染,减少了工序步骤,而且时间上也快很多,投资少、设备占用空间也少,处理能力大。
本发明的第二目的是提供了一种利用上述高效自发结晶的电化学脱盐软化水处理方法软化硬水的装置及其系统,向电解槽中通入电流,使得阴极室内形成强碱性区域,利用电解产生的OH-,使得Ca2+生成CaCO3晶体,与Mg2+生成Mg(OH)2晶体,并随着电解的进行,阴极室pH值增大,CaCO3晶体聚团行为加强而迅速形成晶核,使得过饱和的CaCO3和Mg(OH)2悬浮液高效自发结晶,避免了诱发结晶和外加絮凝剂而带来的二次污染,减少了工序步骤,而且时间上也快很多,投资少、设备占用空间也少,处理能力大。
本发明的技术方案如下:
一种高效自发结晶的电化学脱盐软化水处理方法,包括以下步骤:
(1)通过隔膜或细孔板将电解槽分隔成阳极室和阴极室,并将阳极板和阴极板分别置于阳极室和阴极室中;
(2)通一电流,所述的电流根据I≥1.01Qη(M+2M2)计算得到,其中,I为电极板的电流,单位:A;η为目标软化率,单位:1;Q为阴极室的水流量,单位:L/s;当M0>M1时,M=M0;当M0[(M0+M2)/(M1+M2)]时,M=2M1-M0;M0为待软化水的碱度,单位:mgCaCO3/L;M1为待软化水的钙硬度,单位:mgCaCO3/L;M2为待软化水的镁硬度,单位:mgCaCO3/L;
(3)待软化的水流经阴极室,通电后,在阴极室内形成强碱性区域,体系pH≥10,电解产生的OH-,与HCO3-反应生成CO32-,然后与水体中的Ca2+结合生成CaCO3晶体;与Mg2+结合生成Mg(OH)2晶体,且随电解的进行阴极室pH值的增大,CaCO3晶体的zeta电位降低,晶体聚团行为加强而迅速形成晶核,随高速水流流出阴极室的过饱和CaCO3和Mg(OH)2悬浮液以此晶核为生长点并迅速成长,实现自发结晶,生成为肉眼可见的固体颗粒物,悬浮于水中,再进行沉降或过滤,即完成软化。
优选为,还包括在M0[(M0+M2)/(M1+M2)]时,向阴极液中通入足量空气或二氧化碳。
优选为,常温常压下通入空气的流量根据Q1=0.61Q(M1-M0)计算得到,其中,Q1为向阴极室通入空气的流量,单位:L/s。
优选为,常温常压下通入CO2的流量根据Q0=2.45Q(M1-M0)·10-4计算得到,其中,Q0为向阴极室通入CO2的流量,单位:L/s。
优选为,所述的阳极板为碳电极、贵金属电极或钛基金属氧化物电极中的一种;所述的阴极板为不锈钢、铸铁、石墨、铝或铜等定型导电材料中的一种。
优选为,所述的隔膜为阴离子交换膜、阳离子交换膜、双极膜、石棉纤维膜、无纺布、化纤滤布或陶瓷隔膜中的一种;所述的细孔隔板为带有微小细孔且不影响导电的塑料薄板,如聚四氟乙烯塑料薄板。
本发明还公开了一种利用上述的高效自发结晶的电化学脱盐软化水处理方法软化硬水的装置。
优选为,至少在所述的阴极室的两端分别设有进水口和出水口,在所述的进水口上设有空气或二氧化碳补气口,在所述的出水口上连有过滤器或沉降池。
优选为,在所述的出水口与所述的过滤器或沉降池之间设有第一气液分离器,用来收集绿色能源—氢气。
本发明还公开了一种软化硬水的系统,将若干个上述的电解槽并联、串联或串并复合连接,且在阴极室出水口的汇集处设有第二气液分离器,用来收集绿色能源—氢气。
与现有技术相比,本发明的有益效果如下:
一、本发明的一种高效自发结晶的电化学脱盐软化水处理方法,通过I≥1.01Qη(M+2M2)计算出一适宜电流,使得阴极室内形成强碱性区域,体系pH≥10,利用电解产生的OH-,使得Ca2+生成CaCO3晶体,与Mg2+生成Mg(OH)2晶体,并随着电解的进行,阴极室pH值增大,CaCO3晶体聚团行为加强而迅速形成晶核,流出阴极室的过饱和悬浮液以此晶核为生长点高效自发结晶,实现将水中大部分或全部钙镁离子一次性除去,且在阴极板上不会附着水垢,无需诱发结晶和外加絮凝剂,避免了二次污染,减少了工序步骤,具有软化效率稿,投资少、设备占用空间少,处理能力大等优点;
二、本发明的一种高效自发结晶的电化学脱盐软化水处理方法,还根据Q1=0.61Q(M1-M0)计算通入空气的流量和根据Q0=2.45Q(M1-M0)·10-4计算通入二氧化碳的流量,以提供足够量的HCO3-,达到所需软化率;
三、本发明的一种高效自发结晶的电化学脱盐软化水处理方法,根据通入电流的计算公式和通入空气或二氧化碳的计算公式,计算出电流值及通入空气或二氧化碳的速率,便于实现数控化和自动化,使用清洁电能作为唯一的“处理剂”,无色环保无污染。
氨液分离器为什么正常液位不能超过二分之一
答氨液分离器为什么正常液位不能超过二分之一?不是这样的。氨液分离器的液位不能高于桶面的80%,不能低于30%。氨液分离器用于重力供液系统。对单层冷库可以布置在机房阁楼上或库房穿堂阁楼上,保持液面高于高一层蒸发器排管0.5~2m。当库房为两层或两层,库房氨液分离器距机房教员超过50m,或库房蒸发器为直接膨胀供液时,机房内应设氨液分离器,并且在其下桶。氨液分离器与低压贮液器(或排液桶)之间应设气体平衡管。氨液分离器应超高液位报警装置,设超高液位控制在桶长高度的2/3处。氨液分离器上应设置压力表和安全阀。严禁在氨液分离器的气体进出管之间设旁通阀
制氯乙烯的两种方法
答乙烯氧氯化制氯乙烯
氯乙烯是最重要的单体之一,主要用于生产聚氯乙烯。就产量而言,在乙烯系列高聚物中聚氯乙烯仅次于聚乙烯居第2位。氯乙烯也能与1-1-二氯乙烯、醋酸乙烯、丙烯酸甲酯、丁二烯和丙烯腈等共聚。此外,氯乙烯还用作冷冻剂。
1. 氯乙烯生产方法评述
在氯乙烯生产历史上,曾出现过以下4种生产方法。
(1)乙炔法 这是20世纪50年代前氯乙烯的主要生产方法,中国至今还有一些化工企业仍采用本法生产氯乙烯。
乙炔转化率97%~98%,氯乙烯产率80%~95%,主要的副产物是1-1-二氯乙烷,它是由氯乙烯与过量的氯化氢经加成反应生成的。反应中为保证催化剂HgCl2不被乙炔还原成低价汞盐Hg2Cl2或金属汞,氯化氢是过量的,过量以不超过15%为宜。乙炔法技术成熟,反应条件缓和,设备简单,副产物少,产率高。因为用氯化氢作原料,适合在以氯化氢为副产物的企业(例如电化厂)组织生产。本法的主要缺点是乙炔价贵,催化剂含汞有毒,不仅损害工人身体健康,还会污染环境。
(2)乙烯法 这是20世纪50年代后发展起来的生产方法。乙烯与氯经加成反应生成二氯乙烷:
二氯乙烷再在500~550摄氏度下热裂解或在1.0MPa,140~145摄氏度下经碱分解制得氯乙烯:
乙烯已能由石油烃热裂解大量制造出来,价格比乙炔便宜,催化剂毒害比氯化汞小得多。但氯的利用率只有50%,另一半氯以氯化氢的形式从热裂解气中分离出来后,由于含有有机杂质,色泽和纯度都达不到国家标准,它的销售和利用问题就成为工厂必须解决的技术经济问题,虽然也可用空气或氧把氯化氢氧化成氯气重新使用,但设备费和操作费均较高,导致氯乙烯生产成本提高。
(3)联合法 是上述两法的改良。目的是用乙炔来消耗乙烯法副产的氯化氢。本法等于在工厂中并行建立两套生产氯乙烯的装置,基建投资和操作费用会明显增加,有一半烃进料是价格较贵的乙炔,致使生产总成本上升,乙炔法的引入仍会带来汞的污染问题。因此,本法也不甚理想。
(4)氧氯化法 这是1个仅用乙烯做原料,又能将副产氯化氢消耗掉的好方法。现已成为世界上生产氯乙烯的主要方法。
乙烯转化率约95%,二氯乙烷产率超过90%。还可副产高压蒸气供本工艺有关设备利用或用作发电。由于在设备设计和工厂生产中始终需考虑氯化氢的平衡问题,不让氯化氢多余或短缺,故这一方法又称为乙烯平衡法。很显然,这一方法原料价廉易得、生产成本低、对环境友好。但仍存在设备多、工艺路线长等缺点,需要进一步改进。
2. 氧氯化法工艺原理
1928年德国拉希格(Raschig)公司首先开发成功气相氧氯化法,用来由苯制备氯苯:
这是烃类取代氯化中最早应用的氧氯化法。随后又开发成功液相氧氯化法,转化率和选择性都有很大提高。由于由氯苯制造苯酚的工艺路线在20世纪30年代后逐步被异丙苯自氧化法取代,该法没能得到进一步发展。用该法生产氯苯的工厂也已很少。
氧氯化法在低级烷烃的取代氯化以及乙烯经氯解生成三氯乙烯和全氯乙烯中也有应用,但生产规模都不甚大。
氧氯化法在工业上最成功的应用就是由乙烯和氯化氢生产二氯乙烷,它为氧氯化法在其他氯化领域中的应用展现了良好前景。
(1)化学反应 由乙烯用氧氯化法生产氯乙烯包括乙烯氯化、乙烯氧氯化和二氯乙烷裂解3个工序。在这里仅讨论乙烯氧氯化部分。
氧氯化的主反应为:
氧氯化的主要副反应有3种。
①乙烯的深度氧化
C2H4+2O2→2CO+2H2O
C2H4+3O2→2CO2+2H2O
②生成副产物1.1.2 -三氯乙烷和氯乙烷
此外,尚有少量的各种饱和或不饱和的一氯或多氯衍生物生成,例如三氯甲烷、四氯化碳、氯乙烯、1,1,1-三氯乙烷、顺式1,2-二氯乙烯等,但总量不多,仅为1,2-二氯乙烷生成量的1%。
(3)反应机理 关于乙烯氧氯化反应的机理尽管在国内、外已作了许多研究工作,但至今仍未有定论,主要有以下两种机理:
①氧化还原机理日本学者藤堂、官内健等认为,氧氯化反应中,通过氯化铜的价态变化向作用物乙烯输送氯。反应分以下三步进行:
C2H4+2CuCl2→C2H4Cl2+Cu2Cl2
Cu2Cl2+1/2O2→CuCl2·CuO
CuCl2·CuO+2HCl→2CuCl2+H2O
第1步是吸附的乙烯与氯化铜反应生成二氯乙烷并使氯化铜还原为氯化亚铜。该步是反应的控制步骤;第2步是氯化亚铜被氧化为氯化铜和氧化铜的络物;第3步是络合物与氯化氢作用,分解为氯化铜和水。提出此机理的依据是a)乙烯单独通过氯化铜催化剂时有二氯乙烷和氯化亚铜生成;(b)将空气或氧气通过被还原的氯化亚铜时可将其全部转变为氯化铜;(c)乙烯浓度对反应影响最大。
因此,让乙烯转变为二氯乙烷的氯化剂不是氯,而是氯化铜,后者是通过氧化还原机理将氯不断输送给乙烯的。
②乙烯氧化机理根据氧氯化反应随乙烯和氧的分压增大而加快,而与氯化氢的分压无关的事实,美国学者R.V.Carrubba提出如下机理:
式中a表示催化剂表面的吸附中心;HCl(a),O(a),C2H4(a)表示HCl,O和C2H4的吸附态物种;反应的控制步骤是吸附态乙烯和吸附态氧的反应。
氧氯化早期研究中还有人提出,氯化氢在氯化铜催化下氧化生成氯气,再由氯气与乙烯反应生成二氯乙烷的反应机理。
(3)反应动力学 根据上述反应机理,在氯化铜为催化剂时由实验测得的动力学方法为:
式中:pc,ph,po分别表示乙烯、氯化氢和氧的分压。
由上列2个动力学方法可以看出,乙烯的分压对反应的影响最大,通过提高乙烯的分压可有效地提高1,2-二氯乙烷的生成。相比之下,氯化氢分压的变化对反应的影响则小得多。氧的分压超过一定值后,对反应没有影响,在较低值时,氧分压的变化对反应的影响也是比较明显的。这2个动力学方程式与前述的2种反应机理基本上是吻合的。
(4)催化剂 早期的研究表明,金属氯化物可用作氧氯化催化剂,其中以氯化铜的活性为最高,工业上普遍采用的是负载在γAl2O3、硅酸铝上的氯化铜催化剂。催化剂上铜的含量对反应转化率和选择性都有影响,铜含量增加,转化率提高,但深度氧化生成CO2的量增加,经实验确定,铜含量5%~6%即可。此时,氯化氢转化率可接近100%,生成的CO2量不多。这种单组分催化剂虽有良好的选择性,但氯化铜易挥发,反应温度愈高,氯化铜的挥发流失量愈大,催化剂活性下降愈快,寿命愈短。为了阻止或减少氯化铜催化剂活性组分的流失,在催化剂中添加了第2组分氯化钾,变成双组分催化剂。虽然反应活性有所降低,但催化剂的热稳定性却有明显提高。这很可能是氯化钾与氯化铜形成了不易挥发的复盐或低熔混合物,因而防止了氯化铜的流失。为了提高双组分催化剂的活性,在催化剂中加入稀土金属氯化物,如氯化铈、氯化镧等,既提高了催化活性,又提高了催化剂的寿命,催化剂也就由双组分变为多组分。
图5-2-01 温度对反应影响
图5-2-02
温度对选择性的影响(以氯计)
图5-2-03
温度对乙烯燃烧反应影响
氧氯化反应器有固定床和流化床2种,采用固定床时,将已成型的γAl2O3载体用浸渍法将活性组分浸渍上去,经干燥和通空气活化,即可投入使用。对流化床催化剂,用γAl2O3微球浸渍活性组分。亦可将硅铝酸溶胶与活性组分混合后加入胶凝剂,用喷雾干燥法成型制备流化床微球催化剂。
(5)工艺条件的选择
①反应温度在铜含量为12%(w)的CuCl2/γAl2O3催化剂上研究了反应温度与反应、选择性和乙烯燃烧反应的影响,结果如图5-2-01、图5-2-02和图5-2-03所示。由图5-2-01可见,开始阶段反应随温度的升高而迅速上升,到250摄氏度后逐渐减慢,到300摄氏度后开始下降。因此,反应温度不是愈高愈好,而是有一个适宜范围。由图5-2-02可见,反应选择性在温度上升的开始阶段,也随温度的升高而上升,在250摄氏度左右达到最大值后逐渐下降,这说明,就选择性而言,也有一个适宜范围。图5-2-03示出的是乙烯深度氧化副反应与反应温度的关系。图上曲线表明,270摄氏度前,随反应温度的升高,乙烯深度氧化副反应的增长还比较缓慢,270摄氏度后,乙烯深度氧化则快速增长。从催化剂的使用角度来看,随着反应温度的升高,催化剂活性组分CuCl2因挥发流失的量增加,催化剂失活的加快,使用寿命缩短。从操作安全角度来看,由于乙烯氧氯化是强放热反应,反应热可达251 kJ/mol,反应温度过高,主、副反应,特别是乙烯深度氧化副反应释放出的热量增加,若不能及时从反应系统中移走,由于系统热量的积累,会促使反应温度进一步升高。如此恶性循环,导致发生爆炸或燃烧事故。因此,在满足反应活性和选择性的前提下,反应温度应当愈低愈好。具体的反应温度由选用的催化剂决定,对CuCl2KCl/γAl2O3催化剂而言,流化床使用的温度为205~235摄氏度,固定床为230~290摄氏度。
②反应压力高压对氧氯化法的反应和选择性有不利影响,但在实际的操作温度下,在1.0MPa以下,压力对反应和选择性几乎没有什么影响。因此,选用常压或低压操作均可。考虑到加压可提高设备利用率及对后续的吸收和分离操作有利,工业上一般都采用在低压下操作。
③配料比乙烯、氯化氢和空气之比必须保证使乙烯过量3%~5%。氧也应稍微过量以保证催化剂氧化还原过程的正常进行,但氯化氢不能过量,因为过量的氯化氢会吸附在催化剂表面使催化剂颗粒胀大,视密度减小。如果采用流化床反应器,由于催化剂颗粒胀大会使床层急剧升高,甚至还会发生节涌现象。乙烯不能过量太多,否则会使乙烯深度氧化反应加剧,尾气中CO和CO2增多,反应选择性下降,氧过量太多,也会促使乙烯深度氧化反应的加剧。在原料配比中还要求原料气的组成在爆炸极限范围外,以保证安全生产。工业上采用的配比为:乙烯:氯化氢:氧=1:2:0.5(mol比)。
④原料气纯度采用的空气只需经过滤、洗涤和干燥,除去少量固体杂质和SO2、H2S及水分后即能应用;氯化氢气体由二氯乙烷裂解工序来,常含有乙炔.为此,氯化氢气体与氢气混合后先在一个加氢反应器中脱炔,然后才能进入氧氯化反应器;原料乙烯中的乙炔、丙烯和C4烯烃的含量必须严格控制,因它们比乙烯活泼,也会发生氧氯化反应,生成四氯乙烯、三氯乙烯、1,2-二氯丙烷等多氯化物,给产品的提纯增加难度。同时它们也更容易发生深度氧化反应,释放出的热量会促使反应温度的上升,给反应带来不利影响。一般要求原料乙烯中乙烯含量在99.95%(m)。表5-2-02示出的是中国氯乙烯用原料乙烯的规格。
表5-2-02
中国氯乙烯用原料乙烯的规格
组
分
指
标
组
分
指
标
C2H4
CH4+C2H6
C2H2
99.95%
500 ppm
10 ppm
C2S
S(按H2S计)
H2O
100 ppm
5 ppm
15 ppm
⑤停留时间停留时间对HCl转化率有影响。实验表明,停留时间达10 s时,氯化氢的转化率才能接近100%,但停留时间过长,转化率会稍微下降,这是因为1,2-二氯乙烷裂解产生氯化氢和氯乙烯之故。停留时间过长不仅使设备生产能力下降,而且副反应也会加剧,导致副产物增多,反应选择性下降。
图5-2-04 PPG化学工业公司氧氯化法生产氯乙烯的工艺流程
1.直接氯化反应器;2.气液分离器;3.氧氯化反应器;4.分离器;5.脱轻馏分塔;6.脱重馏分塔;7.裂解炉;8冷塔;9.氯化氢回收塔;10.氯乙烯精馏塔
3. 平衡型氯乙烯生产工艺流程
图5-2-04所示为PPG化学工业公司氧氯化法生产氯乙烯的工艺流程,由于二氯乙烷热裂解产生的氯化氢全部在氧氯化反应中消耗掉,故又称为平衡型氯乙烯生产工艺流程。流程由三大工艺组成:乙烯液相加成氯化生成1,2-二氯乙烷;乙烯气相氧氯化生成1,2-二氯乙烷;1,2-二氯乙烷热裂解生成氯乙烯。
乙烯液相加成氯化的反应条件为:反应温度50摄氏度左右,催化剂为FeCl3,它在氯化液中的浓度维持在250~300 ppm(0.025%~0.03%),乙烯与氯气的摩尔比为1.1:1,即乙烯是过量的。
乙烯气相氧氯化的反应条件为:反应温度225~290摄氏度,压力为1.0MPa,采用CuCl2/γAl2CO3或改良的CuCl2-KCl/γAl2O3为催化剂,催化剂中铜含量在5%~6%(折算成CuCl2为11%~13%),乙烯:氯化氢:氧=1:2:0.5(mol比)。
由加成氯化和氧氯化生成的粗二氯乙烷进入脱轻组分塔和脱重组分塔。轻组分中含有微量氯化氢气体,需经洗涤后方可利用。重组分中含有较多的二氯乙烷,需经减压蒸馏回收二氯乙烷后作进一步处理。所得二氯乙烷纯度很高,可达99%左右。进入热裂解炉,操作条件为:温度430~530摄氏度,压力2.7MPa,催化剂为浮石或活性炭。反应转化率可达50%~60%,氯乙烯选择性为95%,热裂解产物在氯化氢分馏塔蒸出纯度达99.8%的氯化氢,内含炔烃,若有必要,还须经加氢脱炔后才能用作氧氯化原料;在氯乙烯分馏塔中,塔顶馏出纯度为99.9%的成品氯乙烯、塔釜二氯乙烷内含有热裂解生成的重组分,送二氯乙烷精制工序处理。
本流程中采用氧气而不是空气作氧化剂,优点是:反应后多余的乙烯经冷却、冷凝和分离后仍可回氧氯化反应器循环使用,乙烯利用率比空气作氧化剂时高;空气作氧化剂时尾气中乙烯浓度低,仅为1%左右。用焚烧法处理时需消耗燃料,用氧气作氧化剂时,排出的尾气数量很小,但其中乙烯浓度高,用焚烧法处理不需外加燃料;由于配置的原料气中不含氮气,乙烯在原料气中的浓度提高,有利于提高反应和提高催化剂的生产能力,反应器也可做得小一些,从而节省设备制造费用;氧气作氧化剂时由于尾气数量少,不需用溶剂吸收、深冷的办法来回收尾气中少量二氯乙烷,简化了流程,减少了设备投资费用;对固定床反应器而言,氧气作氧化剂时,热点不明显,因而1,2-二氯乙烷的选择性高,氯化氢的转化率亦高,而空气作氧化剂时则相反。表5-2-03列出了两者的比较结果。
表5-2-03
固定床乙烯氧氯化结果比较
乙烯转化为各物料的选择性,%
空气氧氯化法
氧气氧氯化法
1,2-二氯乙烷
氯乙烷
CO+CO2
1,1,2-三氯乙烷
其他氯衍生物
95.11
1.73
1.78
0.88
0.50
97.28
1.50
0.68
0.08
0.46
HCl的转化率,%
99.13
99.83
现在,有不少大型化工企业都建有空气分离装置,氧气的供应已不存在问题,这为氧气作氧化剂的乙烯氧氯法提供了发展良机。氧气氧氯化法的消耗定额(以生产1 t二氯乙烷为基准)为:乙烯(100%)287 kg,氯化氢(100%)742 kg,氧气(100%)177 kg。
图5-2-05所示为氧氯化法生产氯乙烯的物料平衡图。
图5-2-05 平衡型的氯乙烯生产组织形式*
图中的数字是各种物料的实际重量比例数
4. 氧氯化反应器
不论是空气氧氯化还是氧气氧氯化,都可采用固定床或流化床反应器。
(1)固定床氧氯化反应器
图5-2-06
流化床乙烯氧氯化反应器构造示意图
1.乙烯和HCl入口;2.空气入口;3.板式分布器;4.管式反应器;5.催气剂入口;6.反应器外壳; 7.冷却管组;8.加压热水入口;9、11、12.旋风分离器;10.反应气出口;13.人孔;14.高压水蒸气出口
这种反应器结构与普通的固定床反应器基本相同,内置多根列管,管内填充颗粒状催化剂,原料气自上而下流经催化剂层进行催化反应。管间用加压热水作载体,副产一定数量的中压水蒸气。
固定床反应管存在热点,局部温度过高使反应选择性下降,活性组分流失加快,催化剂使用寿命缩短,为使床层温度分布比较均匀,热点温度降低,工业上常采用三台固定床反应器串联:氧化剂空气或氧气按一定比例分别通入三台反应器。这样每台反应器的物料中氧的浓度较低,使反应不致太剧烈,也可减少因深度氧化生成的CO和CO2的量,而且也保证了混合气中氧的浓度在可燃范围以外,有利安全操作。
(2)流化床氧氯化反应器 流化床反应器反应温度均匀,不存在热点,且可通过自控装置控制进料,使反应器温度控制在适宜范围内。因此对提高反应选择性有较大好处。反应产生的热量可用内设的热交换器及时移走。流化床氧氯化反应器的构造示意于图5-2-06。
空气(或氧气)从底部进入,经多喷嘴板式分布器均匀地将空气(或氧气)分布在整个截面上。在板式分布器的上方设有C2H4和HCl混合气体的进口管,此管连接有与空气分布器具有相同数量喷嘴的分布器,而且其喷嘴恰好插入空气分布器的喷嘴内。这样就能使两股进料气体在进入催化床层之前在喷嘴内混合均匀。
在反应段内设置了一定数量的直立冷却管组、管内通入加压热水,籍水的汽化以移出反应热,并副产中压蒸气。在反应器上部设置三组三级旋风分离器,用以回收反应气夹带的催化剂。催化剂的磨损量每天约为0.1%,需补充的催化剂自气体分布器上部用压缩空气送入反应段。
由于氧氯化有水产生(乙烯深度氧化也有水产生),如反应器的一些部位保温不好,温度过低,当达到露点温度时,水就会凝结出来,溶入氯化氢气体生成盐酸,将使设备遭受严重腐蚀。因此反应器的保温相当重要。另外,若催化剂表面粘附氧化铁时,氧化铁会转化为氯化铁,它能催化乙烯的加成氯化反应,生成副产物氯乙烷(CH3CH2Cl)。因此,催化剂的贮存和输送设备及管路不能用铁质材料。
今天的内容先分享到这里了,读完本文《广西钢衬四氟气液分离器 广西甲烷压缩机气液分离器》之后,是否是您想找的答案呢?想要了解更多,敬请关注www.zuqiumeng.cn,您的关注是给小编最大的鼓励。
本文来自网络,不代表本站立场,转载请注明出处:https://www.zuqiumeng.cn/wenda/359782.html